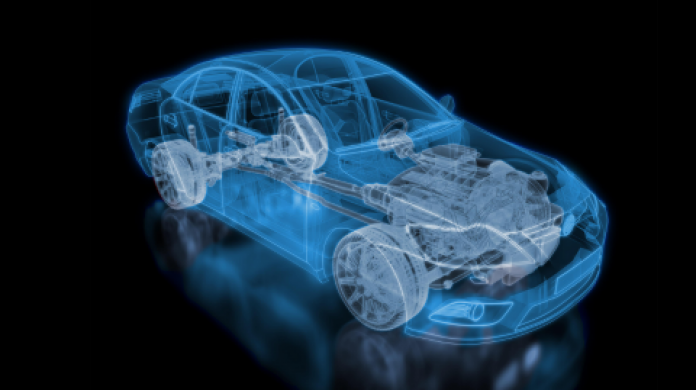
With the adoption and continued growth of electrified powertrains and autonomy the automotive industry is in the middle of a profound transformation. Never before have manufacturers needed to develop so much new technology and it is driving the demand for a more efficient way of testing. At the forefront of this transformation is XiL testing (Everything-in-the-Loop), which encompasses Software-in-the-Loop (SiL), Hardware-in-the-Loop (HiL), Driver-in-the-Loop (DiL) and Vehicle-in-the-Loop (ViL). In this latest blog post, Matt Dustan, AB Dynamics Director, Laboratory Test Systems, explains what exactly XiL is and its potential to reduce the need for prototype vehicles, improve safety, and evaluate the interaction of interconnected systems.
What is XiL?
XiL testing essentially allows the integration of external elements into a simulation to enable a system or sub-system to be thoroughly evaluated. One of the key advantages of XiL testing is the ability to test hardware and software in parallel before transitioning to a prototype vehicle. This early-stage testing enables manufacturers to identify issues and make critical design decisions earlier in the development process than would be possible without XiL testing. The result? Engineering is front-loaded much earlier in the development process to lead to a more mature solution before progressing to prototype vehicles, significantly reducing time-to-market and lowering costs.
In the earlier stages of development, simplified simulations and models can be used but as the design matures it is critical to make them as accurate as possible. Using real hardware in the loop is crucial for achieving precise feedback and accurate correlation between simulations and reality and this is where HiL comes into play. It enables real complete sub-systems to be integrated into the development process, providing precise feedback, and ensuring that simulations correlate with real-world performance.
Interconnected system development
XiL testing also excels in evaluating the interaction of interconnected automotive systems. For instance, our SSTM (Steering System Test Machine) enables a complete steering system to be evaluated and thoroughly tested. Through XiL testing, real steering hardware and software can be assessed using a simulated vehicle model.
As the SSTM is DiL capable, test drivers can provide valuable subjective feedback on steering feel. Previously, this would only be possible once the steering system was fitted into a prototype vehicle much further down the development cycle. Correcting any issues that arise at this stage could be hugely costly. Using the SSTM to evaluate the sub-system as soon as it is available from the supplier helps to de-risk the programme.
Reducing prototypes and improving safety
XiL testing has become vital in improving the robustness of emerging technologies, such as autonomous systems. By collaborating with automotive manufacturers, we have seen the transformative impact of XiL testing in taking immature software toolchains and rapidly enhancing their robustness in a controlled laboratory environment. This not only accelerates development but, particularly in the case of autonomy, reduces the need for extensive on-road testing to improve safety.
The holy grail for the automotive industry is to remove the prototype vehicle stage altogether. Huge investments are made by manufacturers at this point in the programme. We are already seeing stages of prototyping being reduced as a result of simulation and XiL testing, particularly at the sub-system level. However, correlating your simulations with real-world tests is the only way to be truly confident in the results of simulations, so final prototypes are likely to remain a part of the development process for the foreseeable future.
Limitations and the future of XiL testing
There are also certain areas of vehicle development that remain incredibly difficult to simulate accurately in real-time. For example, modelling the behaviour of materials like rubber is complex. As a result, NVH (Noise Vibration and Harshness) is challenging to get right in simulation and as squeaks and rattles can be a common source of warranty issues, it wouldn’t be wise to rely on simulations to validate this. However, we are seeing OEMs actively developing specialised test rigs to better understand and address these complex material interactions.
As the XiL testing process evolves, we are witnessing a shift towards parallel testing, where HiL, SiL and DiL are being utilised at the same time. We are also seeing a move to cloud computing to significantly increase the scale of simulations. The ability to access sophisticated computing power from external providers, hosted in the cloud, is becoming increasingly attractive. This approach is particularly beneficial for automotive startups, allowing them to avoid upfront investment costs and scale their computing resources as needed.
Conclusion
Ultimately, XiL testing is a catalyst for transformation across the automotive industry. It is a critical tool for streamlining development processes, reducing costs and in some cases improving safety. As the industry continues to adopt increasingly sophisticated technologies, XiL testing is now at the forefront of helping manufacturers achieve this in a cheaper, quicker, and more robust way.
The AB Dynamics Group is perfectly placed to support this process as a supplier of products and solutions across the XiL spectrum. With the SSTM and our SPMM, AB Dynamics is providing the industry with state-of-the-art HiL test equipment to thoroughly test and correlate vehicle subsystems. Ansible Motion provides a range of high-fidelity DiL simulators and sister company and simulation software specialist, rFpro, creates highly realistic digital environments for all this testing to take place within.
Key takeaways
As the industry progresses towards virtual development and validation XiL testing will play a key role in providing manufacturers the confidence to remove stages of physical prototypes:
- XiL testing enables the engineering of systems and sub-systems to be frontloaded, reducing cost and accelerating time to market.
- Parallel testing provides highly valuable subjective feedback with the real hardware.
- Some aspects of vehicle development, such as NVH, are challenging to simulate accurately providing a barrier to the complete removal of physical prototypes.
- Advances in cloud computing are allowing testing to be massively scaled and provide start-ups with significant testing capability.
For more information on AB Dynamics' SSTM machine, download our brochure.