This year AB Dynamics and its sister company Dynamic Research Inc. (DRI) celebrate the 10th anniversary of the first sale of the Guided Soft Target (GST) surrogate vehicle target system. In this blog, Joseph Kelly, Chief Engineer at DRI, explains how the GST has set the global standard for 3D vehicle targets and has helped to revolutionise the testing and development of lifesaving ADAS technologies.
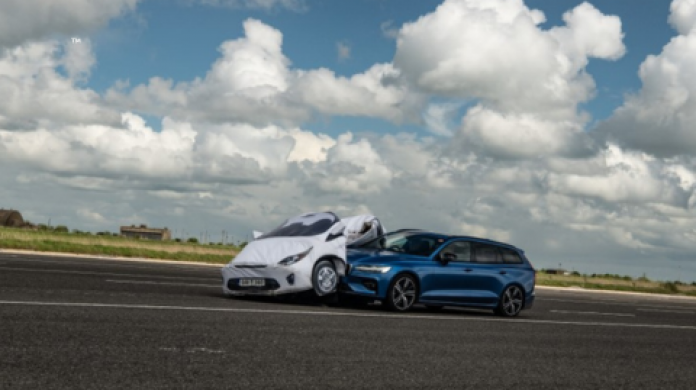
The GST test system consists of the Soft Car 360, an impactable dummy vehicle target attached to a low-profile robotic platform designed to be run over by vehicles. In this article, we will be looking at the origins of the GST and the industry trends that have shaped its design.
The history of the GST
The GST’s story starts in 2007 when crash avoidance technologies, such as Automatic Emergency Braking (AEB), were still in their infancy and so too were the systems to test them. A variety of targets, ranging from simple radar reflectors to partial vehicle representations (both static and dynamic), were developed to aid in the evaluation of rear end collision avoidance and mitigation systems, but these had limitations restricting approach speeds and angles, as well as lateral offsets. Additionally, some of the dynamic systems required the presence of other vehicles to tow the targets, or suspend them from above, which could sometimes adversely affect the performance of the vehicles under test.
It was at this time that DRI collaborated with NHTSA (National Highway Traffic Safety Administration) on the ACAT (Advanced Crash Avoidance Technologies) project, together with Honda. The project aimed to develop practical methods for evaluating the effectiveness of emerging ADAS technologies. A key phase of the project was to establish the test requirements in order to conduct full-scale testing of the technologies.
The project identified three key vehicle-to-vehicle scenarios that would need to be tested, which were head on, rear end and crossing paths.
These tests necessitated a dynamic solution that was strikeable from multiple angles that:
- Did not damage the vehicle during test,
- Did not present a safety risk to test personnel,
- Was easily reconfigurable and enabled close coordination of vehicles with regard to conflict conditions such as closing speed and angle, and
- Could easily be reset after impact for further testing.
The solution: the GST system. Through this project, DRI became fundamental in finding ways to help the industry test and develop first-generation collision avoidance systems that have since been developed into today’s technologies.
The initial development of what would become recognisable as the GST system used a simple vehicle target constructed from foam, fitted to a first-generation version of the GST platform, which was affectionately known internally as the ‘Turtle’. It was the first self-propelled dummy vehicle target that could be safely run over, providing unrivalled testing flexibility. Designed initially for detection by lidar, the system’s visual representation of a vehicle and its radar reflectivity were less relevant. The entire system was designed and manufactured in-house at DRI, including the platform’s navigation and control system.
DRI recognised that the appearance and durability of the target needed to be improved to be useful to manufacturers using camera and radar systems and this formed the core development path for the following few years. A project with IIHS (Insurance Institute for Highway Safety) in 2011 and feedback from other industry experts identified a demand for stable radar reflectivity, which resulted in the introduction of a new reflective material for the Soft Car 360. Other developments included enclosing the foam skins in vinyl fabric “pillowcases”, which allowed the application of photorealistic graphics and increased durability and realism. The result was a first-generation version of the Soft Car 360 that we know and recognise today.
DRI’s involvement in these industry projects led to the development of equipment that is now in use globally to thoroughly test ADAS technologies. Worldwide adoption of standardised tests that rely on this equipment is helping to provide safety ratings of new vehicles to educate consumers and improve road safety.
In 2012 DRI developed what became the first commercially available GST that incorporated all the various features to make it representative to a variety of sensor systems. Later that year, DRI began its partnership with AB Dynamics to further develop the product and the first unit was delivered to an Asian OEM in 2013.
This partnership allowed customers to experience AB Dynamics’ tried and tested control hardware and software from the steering and pedal robots in a driverless platform. It also allowed for seamless synchronisation between robots thanks to AB Dynamics’ patented Synchro software.
In 2014, DRI developed the second generation GST in collaboration with NHTSA. This project involved reducing the radar reflectivity of the platform and increasing the acceleration and top speed, to cater for the growing variety of tests being carried out. There was also a heavy-duty version developed for trucks. In 2018, AB Dynamics introduced the MK2 GST platform, bringing improvements to the market, such as a lower overall profile, 100 km/h top speed and improved path following.
The collaboration between AB Dynamics and DRI proved to be a great success resulting in the GST’s approval for use by Euro NCAP and NHTSA as its Global Vehicle Target in 2018. The relationship further strengthened when DRI joined the AB Dynamics group through an acquisition in 2019.
In 2020, during the COVID-19 pandemic, AB Dynamics introduced the GST 120, the highest top speed GVT on the market. This was an incredible engineering achievement as although a 20 km/h increase in speed doesn’t seem much, an astounding 70% increase in power is required. Alongside its increased top speed, an Anti-lock Braking System (ABS) was also introduced, which later became standard on all GST products.
Since its initial introduction the GST has been continually developed, particularly to improve its realism in line with the increasing sophistication of ADAS perception and classification technologies, and the Soft Car 360 is currently in its seventh revision.
Industry drivers and challenges
When the GST was first introduced ten years ago, advanced crash avoidance technologies were usually found on higher-end luxury vehicles. Thanks, in part, to the ACAT projects these technologies were becoming more mainstream and Volvo was the first OEM to fit AEB as standard on all new models in 2014. The continued development of these technologies and an increased focus on safety regulations has driven the mass adoption of collision avoidance and mitigation systems.
One of the most used sensor systems is radar. It scans the world very efficiently but often lacks definition and is limited in providing data on verticality, which would be useful in correctly classifying objects. Increasing the resolution of radar systems is a key area for development for OEMs. The GST system has been future-proofed in this respect as the GST platform has been designed to minimise radar reflectivity, whilst the Soft Car 360 has been optimised from top to bottom to reflect radar realistically.
Although very efficient in the way it transmits and receives data, radar does have its limitations. As a result, OEMs are now moving towards sensor fusion, combining a variety of sensors to more accurately perceive the world ahead. For example, a camera and radar system sense the world in disparate but complementary ways leading to a much better perception system than would be possible from a single type of sensor.
As these technologies have matured and adoption has increased, the challenge for the industry has shifted from simply avoiding and mitigating a potential crash to them being more usable on the road and not issuing false positives. This is critical in translating these technologies into real world road safety improvements.
To achieve this the vehicle must correctly discern what it can and can’t ‘drive into’. A good example of this problem are steel trench plates, used for covering up holes or trenches in the road during road works. They are large and reflective to a radar system, just like a car, so they could be mistakenly perceived as a parked car, as a result, vehicles could apply full braking as they approach. This is where a combination of sensor systems should be able to correctly identify the object and make the correct decision to not intervene.
The future of the GST
These industry trends have driven the development path of the GST system. The Soft Car 360 has been developed in collaboration with industry partners, including sensor manufacturers and OEMs, through workshops coordinated by Euro NCAP, NHTSA, and IIHS. This collaboration has been critical in improving the realism of the target and understanding how it is perceived by the many different sensor technologies used on a vehicle.
Additionally, the quantity and complexity of ADAS testing is expected to continue to grow exponentially and so too are the tools used to test these systems. The hatchback version of the GST has been approved for use in NCAP tests since 2018 but there is a range of vehicle targets available, including a micro, sedan and estate version. This range will continue to expand to provide customers with the variety required to thoroughly test a vehicle’s sensor system.
One of the next big steps in active collision avoidance technologies is likely to come from increased connectivity. The ability for a vehicle to communicate with infrastructure and other vehicles around it increases awareness of potential dangers and the time to react. The integration of connectivity, or V2X (Vehicle-to-Everything), will significantly impact the testing landscape. AB Dynamics is participating in the SECUR project (Safety Enhancement through Connected Users on the Road), which aims to create a coherent proposal for V2X testing and assessment protocols for Euro NCAP. AB Dynamics’ key input into the project is to help define a specification for connected targets to support V2X testing in the future.
The GST timeline:
- 2007 – DRI starts collaboration with Honda and NHTSA on the Advanced Crash Avoidance Technologies (ACAT) project.
- 2008 – DRI develops the Low-Profile Robotic Vehicle (LPRV) ‘Turtle’, an early version of what would become the GST platform, and a simple Soft Car 360.
- 2010 – DRI continues development of the Soft Car 360, integrating a multi-panel construction design.
- 2012 – DRI signs collaborative agreement with AB Dynamics.
- 2013 – First GST delivered to customer.
- 2014-2015 – The second generation GST is developed for NHTSA, including heavy duty truck compatibility.
- 2018 – The GST is approved as the official Global Vehicle Target (GVT) by NHTSA, IIHS and Euro NCAP. The GST MK2 platform introduced with various improvements, higher top speed (100 km/h) and lower overall height.
- 2019 – DRI acquired by AB Dynamics.
- 2020 – AB Dynamics becomes a partner in the SECUR project featuring the GST system. The GST 120 introduced, the fastest GVT in the market, with a top speed limited to 120 km/h. Also introducing improved path following at high speeds as well as ABS to the GST line up.
- 2022 – GST 120 and Soft Car 360 were officially approved by Euro NCAP under Technical Bulletin 29.
- 2023 – It is the ten-year anniversary of the delivery of the first GST. GST and V2X demonstration for the SECUR project.
For more information on the GST test system or to arrange a demo, contact us at info@abdynamics.com