Euro NCAP has announced its new provisional 2026 protocols, which are set to introduce updated requirements for Advanced Driver Assistance Systems (ADAS), driver monitoring, crash avoidance, and post-crash safety. These changes aim to set higher standards for vehicle safety, requiring manufacturers to adapt their validation methodologies and testing strategies to meet the revised criteria.
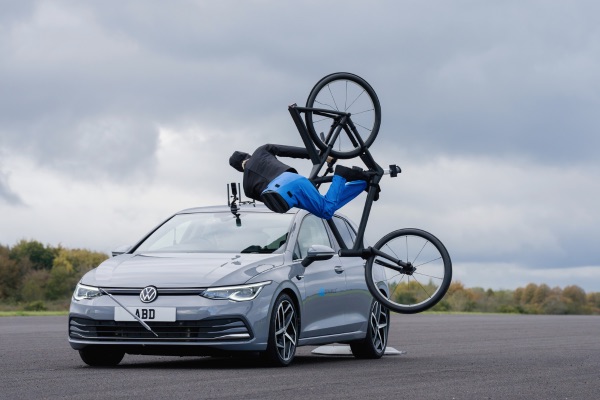
Strengthened driver monitoring and HMI testing
One of the most notable changes in the 2026 update is the expanded assessment of driver monitoring systems. Vehicles will now be required to detect signs of drowsiness, distraction, and potential substance impairment through behavioural analysis, including steering patterns, eye tracking, and reaction times. This places greater emphasis on integrating robust in-vehicle monitoring technologies that provide real-time feedback and intervention.
Additionally, Euro NCAP is introducing Human-Machine Interface (HMI) testing, evaluating the accessibility and usability of essential vehicle controls. This requirement has largely been introduced due to the widespread adoption of touchscreens, which has led to drivers taking longer to perform basic tasks when compared to traditional buttons. This change ensures that drivers can intuitively operate functions such as the horn, windshield wipers, and indicators without unnecessary distraction.
Post-crash safety and EV-specific requirements
The 2026 protocol extends its scope to place new requirements on post-crash safety. Vehicles must now provide standardised ‘Rescue Sheets’ and upgraded eCall systems that transmit critical crash data to emergency services. These improvements ensure that first responders receive timely and precise information to help facilitate the rescue operation.
For electric vehicles (EV), Euro NCAP is introducing additional post-crash safety requirements, including thermal runaway detection systems designed to mitigate battery-related hazards. EVs will need to maintain a minimum of 90 minutes of post-crash safety, providing emergency responders with a critical window to safely extricate occupants.
More rigorous ADAS performance evaluations
Euro NCAP’s new protocols elevate the standards for ADAS reliability and responsiveness. Systems like Adaptive Cruise Control, Speed Assistance, and Steering Assistance will undergo more exhaustive scrutiny to ensure they operate effectively and transparently. These tests aim to prevent over-reliance on automation while reinforcing the role of the driver in maintaining vehicle control.
Enhanced crash avoidance and protection measures
Euro NCAP is broadening its crash avoidance testing to include a wider range of frontal impact scenarios, lane departure events, and low-speed collision situations. As a result, ADAS engineers must develop increasingly sophisticated perception and response systems to detect and mitigate collision risks in more complex environments.
The impact on ADAS development
These changes underscore the increasing quantity and complexity of ADAS testing and validation. Engineers must now ensure that systems perform reliably across a broader range of scenarios, requiring extensive real-world and virtual validation.
At AB Dynamics, we continue to support the industry in meeting these evolving safety standards. Our advanced track testing systems, driving robots, and simulation solutions help engineers rigorously test and validate ADAS technologies, ensuring compliance with the latest Euro NCAP protocols. As the 2026 requirements come into effect, our expertise in controlled, repeatable testing environments will be instrumental in helping manufacturers navigate this evolving landscape.
Euro NCAP 2026 protocol updates summary
Safe Driving
- Driver Monitoring Systems (DMS): Expanded to detect impairments like alcohol or drug use through behavioural indicators, not just drowsiness or distraction.
- Human-Machine Interfaces (HMI): New protocols assess cockpit controls for accessibility, positioning, and tactile feedback.
- Adaptive Safety Features: Allowance has been made for Lane Keeping Assist systems that adjust in real-time based on driver alertness and distraction levels, helping to improve driver acceptance.
Crash Avoidance
- Real-World Scenarios: Evaluation includes frontal impacts, lane departures, low-speed collisions, and emergency interventions while considering driver intention and distraction levels.
- Collision Warnings: Enhanced focus on the acceptability and effectiveness of warnings and emergency interventions.
Crash Protection
- Occupant Diversity: Includes older or smaller occupants in test configurations, with improved protection for children via new Lower Tether systems for child seats.
- Rollover Situations: Expanded occupant protection in rollover scenarios.
- Human Body Models (HBM): Introduction of advanced simulations for diverse occupant morphologies and configurations.
Post-Crash Safety
- Rescue Information: Points awarded for Rescue Sheets and Emergency Response Guides adhering to ISO 17840 standards.
- Advanced eCall Systems: Must transmit detailed crash data, including vehicle location, occupant count, and type of impact.
- Extrication Protocols: Updated procedures for energy isolation, occupant release, and window accessibility. Electric vehicles must include thermal runaway detection systems that prevent hazardous conditions for at least 90 minutes.
For more information on how AB Dynamics can support your Euro NCAP testing, click here.
AB Dynamics specialises in the design and manufacture of K&C (kinematics and compliance) test machines for the automotive industry. In this blog post Matt Dustan AB Dynamics Director, Laboratory Test Systems, does a deep dive into this technology. He explains exactly why K&C test machines were developed and what they are used for, how virtual testing integrates with them, and what the future of K&C testing holds.
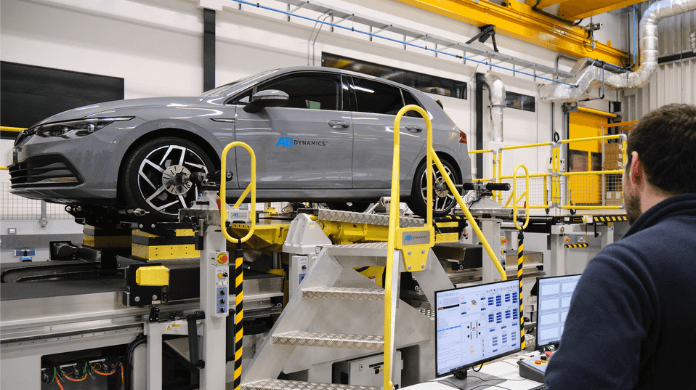
How does K&C testing work?
Before the existence of K&C test machines, there was no standardised method for comprehensively generating the kinematics and compliance characteristics of a vehicle’s suspension system. Instead, to develop physical design adjustments, dynamics engineers had to rely heavily on matching subjective track evaluations with their own experience. K&C machines changed the game by making standardised, objective assessment possible and practical. In essence, a K&C test machine applies very accurate movements and forces into a vehicle’s suspension system. The resulting data provides engineers with a thorough understanding of a vehicle’s ride and handling characteristics.
In most instances, a K&C machine will clamp onto the vehicle’s body and manipulate the vehicle’s wheels to provide the necessary inputs. This enables a combination of roll, pitch, bounce and yaw motion to be applied to the vehicle body to simulate cornering, braking and traction.
However, at AB Dynamics, we do things a little differently. Our K&C test machine, the SPMM, is unique in that instead of moving the vehicle’s wheels to apply the required inputs, it moves the vehicle body, and the wheels remain relatively static. This moving centre table design means the ground plane, which in this case is the road, remains fixed. This more faithfully replicates what happens in the real world because roads don’t move! We can confidently say that this approach results in more accurate data.
What types of K&C tests are there?
There are hundreds of tests that can be conducted on our K&C machine. Some of the industry standard tests include bounce and bounce-pitch, roll, steering, cornering, braking, traction, and lateral and longitudinal compliance. But we also work closely with our customers to create bespoke tests too. For example, horizontal simulation tests that aim to determine the individual contributions of kinematics and compliance effects during lateral and longitudinal manoeuvres, such as cornering and braking.
What are kinematics and compliance test machines used for?
There are lots of use cases for a K&C test machine, it really is a multi-faceted tool. One of the most common use cases is to benchmark competitor vehicles to thoroughly understand the handling characteristics and determine trends in the market. It can be used throughout the vehicle development process to assess suspension systems. It is also used to monitor the performance of early production vehicles to ensure they remain within the prescribed tolerances.
One of our first K&C machines, was installed at Horiba MIRA in 1995 and has tested in excess of 3,000 vehicles, helping to develop next-generation vehicles. Another, being used by a Chinese vehicle manufacturer, is processing more than 150 vehicles every year, including benchmarking and vehicle development activities.
What about virtual K&C testing using simulation?
To do this a multibody simulation (MBS), also referred to as multibody dynamics (MBD), is required. It is a computer-aided engineering (CAE) method used to simulate and analyse the behaviour of mechanical systems. In vehicle dynamics and K&C testing, it replicates a suspension system by modelling interconnected rigid or flexible components linked through joints and actuators. These components interact and move based on applied forces, just as they would during real-world K&C testing, but in a virtual environment.
How does physical K&C testing integrate with MBS?
K&C testing is essential for MBS as it provides real-world data on how a specific vehicle’s suspension performs under various forces. The K&C data allows the MBS model to be correlated to real-world scenarios, ensuring the virtual simulations are highly accurate.
MBS software, such as RACE (Rapid Axle Concept Evolution), offers a cloud-based solution where physical K&C data can be integrated seamlessly. The tests performed virtually in RACE correspond directly to those conducted on AB Dynamics K&C machines, ensuring a precise match between physical and simulated results. This allows engineers to replicate real-world conditions within the virtual environment, fine-tune suspension parameters, and analyse vehicle performance across a range of scenarios.
What is the future of K&C testing and how is it changing?
We are seeing more manufacturers adopting virtual test and validation processes to help accelerate the development of new vehicles. As a result, simulation and digital vehicle models are now critical tools in the development process but correlation with the real world is critical to success. K&C test machines are now being used to generate all the chassis-based data required to create high-fidelity vehicle models.
On top of this, vehicles are also being integrated into Hardware-in-the-Loop (HIL) simulation testing using K&C test machines. This enables a physical vehicle or sub-system of a vehicle to be tested with the resulting data being fed in real-time to an external simulation environment. This is particularly useful for the development of active and semi-active chassis control systems.
K&C testing has been a fundamental stage of automotive development for decades now and with the increasing importance of virtual development and the integration of HiL this is unlikely to change anytime soon.
Key takeaways
- K&C test machines apply very accurate movements and forces into the vehicle’s suspension system
- AB Dynamics’ SPMM K&C test machine is unique as it moves the vehicle body whilst the wheels remain relatively static, therefore faithfully simulating on-road vehicle behaviour
- K&C machines allow an MBS model to be correlated to real-world data, ensuring the virtual simulations are highly accurate
- Manufacturers are increasingly adopting virtual test and validation processes to help accelerate the development of new vehicles
- Vehicles are also being integrated into Hardware-in-the-Loop (HIL) simulation testing using K&C test machines
For more information on our K&C test machines, click here.
Earlier this year, NHTSA's FMVSS 127 rule mandated that all cars and light trucks sold in the US must be fitted with AEB (Automated Emergency Braking) from 2029. In this roundtable discussion with AB Dynamics’ Director of Track Testing, Dr Andrew Pick (AP), and DRI’s Director of Track Testing, Nadine Wong (NW), we take an in-depth look into how OEMs and test houses can get ahead of FMVSS 127.
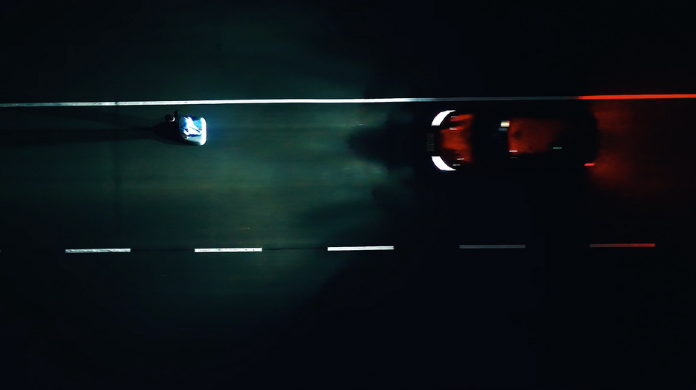
AEB is a recognised and established technology, what does the current landscape look like in the US?
NW: Exactly, there is nothing new about AEB. In fact, around 90%of new passenger vehicles in the US are offered with the technology. FMVSS 127 is aiming to not only increase this to 100%, by making it mandatory, but it is also requiring that the performance and capability of these systems be improved, which is reflected in the testing requirements.
ABD: So what exactly is FMVSS 127 and what capabilities is it aiming to improve?
AP: FMVSS 127 (Federal Motor Vehicle Safety Standard) is a regulation mandating that passenger vehicles and trucks in the US must be fitted with AEB as standard by 2029. Specifically, it states that vehicles have an AEB system and FCW (Forward Collision Warning) that operate at any forward speed greater than 10 km/h (6 mph) and less than 145 km/h (90 mph). The AEB system should be capable of preventing collisions with stationary objects at speeds up to 100 km/h (62 mph) and detecting pedestrians in both daylight and darkness. In addition, the standard requires that the FCW system provides an auditory and visual warning to the driver to apply the brakes up to 145 km/h (90 mph) when a collision with a lead vehicle is imminent, while automatic braking is required up to 73 km/h (45 mph) when a pedestrian is detected.
That sounds like a demanding set of requirements for manufacturers to meet, is FMVSS 127 achievable?
NW: We have already conducted extensive FMVSS 127 testing for clients and regularly work directly with NHTSA to test and develop new protocols, so DRI has a lot of experience in this area. We know that there are vehicles currently available that already come close to achieving the standard. In our experience, the more challenging area is the nighttime PAEB (Pedestrian Automatic Emergency Braking) tests, this is likely to require further advancements and developments in sensor technologies.
AP: Luckily, OEMs currently have five years to achieve these required advancements. The combination of high-speed tests as well as detecting pedestrians at nighttime may require more sophisticated sensor systems than are commonly used today, such as long-range radar and LiDAR.
What specifically is driving the need for more advanced sensors, why is it more challenging?
NW: The high-speed nature of these tests is certainly one of the key challenges. The 90 mph (145 km/h) test dictated by FMVSS 127 is one of the highest mandated test speeds globally for active safety systems. It significantly increases the required field of view of sensors, as well as the braking distances involved. This also has implications for the practicalities of testing; necessitating more room to get the vehicle up to speed and the increased potential for damage caused to the vehicle under test and other test equipment.
AP: As Nadine previouslymentioned, perhaps the main challenge is the PAEB tests at nighttime. While some Euro NCAP night tests allow for street lighting, FMVSS 127 mandates testing in complete darkness and in the most challenging cases low beam lighting only to illuminate the scene ahead. This makes detecting the pedestrian more difficult for sensor systems.
NW: And to top it off, FMVSS 127 requires a 100% pass rate, leaving no room for error, unlike other international AEB standards that allow for a margin of acceptable failure.
How does the regulation compare with its European counterparts?
AP: You can make the argument that FMVSS 127 is one of the most challenging active safety regulations to achieve. The equivalent standard in Europe is the UNECE R152 regulation, which is a mandatory requirement that came into force in 2020. FMVSS 127 has requirements up to 145 km/h (90 mph), while UNECE R152 is limited to just 60km/h (37mph). FMVSS 127 mandates a non-contact result, or complete collision avoidance, while in comparison UNECE allows for collision mitigation as well as avoidance. Also applicable in the region, although not mandatory, is Euro NCAP’s set of AEB protocols.
What’s more challenging; NHTSA’s FMVSS 127 or Euro NCAP’s AEB protocol?
NW: NHTSA is certainly raising the bar with FMVSS 127. On the face of it FMVSS 127 is more challenging. Euro NCAP test speeds are limited to just 80 km/h (50 mph) and, similar to R152, collision mitigation is acceptable, and a 100% pass rate is not required. However, where Euro NCAP’s AEB protocols are more challenging to meet is they cover a much broader range of speeds and scenarios. For example, the inclusion of cyclists, motorcyclists, turning at intersections, curved roads and lane changes. This necessitates sideways-looking sensors and a more discerning AEB system.
So that’s why achieving the protocol is challenging but how about conducting the testing itself, will FMVSS 127 require a new approach on the test track?
NW: At DRI, we have developed a very flexible test methodology that enables us to accommodate a broad range of tests. We have adapted our approach to accommodate FMVSS 127 and we have experience conducting the tests for customers.
However, the high-speed nature does necessitate additional track. Getting an average family car from 80-140km/h (50-87mph) can add 200-300m to the required space. The speed also makes the use of an automated abort procedure preferable during repeated testing to avoid having to constantly reassemble impacted ADAS targets.
How does the abort procedure work?
AP: We have developed an automated abort manoeuvre procedure, which can be programmed into our software. We can do this because our system closely controls and coordinates both the vehicle under test through our driving robots and the test objects via our LaunchPad and GST test platforms. When the AEB system doesn’t intervene before a collision is imminent our software can automatically take action to either brake or steer to avoid or mitigate a collision. When vehicle speeds are in excess of 145 km/h (90 mph) this abort manoeuvre could be critical in keeping a test programme on schedule.
NW: We use this system at our proving ground in California to reduce downtime and maximise test efficiency, which is crucial to a successful test programme. To further increase efficiency, we are also working with AB Dynamics to create, test and validate the FMVSS 127 ‘Special Group’ to automate more of the test programme.
How do the ‘Special Groups’ help with testing?
AP: Our Special Groups are a library of pre-defined test scenarios. Combined with our driving robots, ADAS targets and other track test equipment, it enables test engineers to automate the creation, set-up, variation, execution and verification of industry-standard active safety protocols. The FMVSS 127 Special Group is currently being trialled with DRI and will be available to customers soon.
NW: It saves us a lot of time at the track and provides a real-time pass or fail, which is incredibly useful in planning what scenario to conduct next.
Finally, what should OEMs be doing to get ahead of FMVSS 127?
AP: Start testing sooner rather than later! OEMs need to understand where they fall short on the regulation and why, and the best way to do that is to test with current vehicle models to see how they stack up. This will help them to focus development to ensure they are ready for 2029.
NW: I agree with Andrew,and we are already experiencing an increase in enquiries from OEMs looking to do just that.
Key Takeaways
- High-speed collision avoidance: FMVSS 127 mandates that AEB systems must prevent collisions with stationary objects at speeds up to 100 km/h (62 mph) and apply the brakes automatically up to 145 km/h (90 mph), significantly increasing the operating domain for AEB.
- Nighttime testing challenges: Unlike Euro NCAP, FMVSS 127 includes testing in complete darkness with only vehicle lighting, significantly increasing the challenge of pedestrian detection.
- Stringent pass requirements: FMVSS 127 requires a 100% pass rate for a mandated test, leaving no room for error, in contrast to other standards that allow some failures.
- Technological advancements needed: FMVSS 127 pushes the boundaries of what is possible from current AEB technologies. More sophisticated sensor systems, such as long-range radar and LiDAR, may be required by 2029.
- Get ahead of FMVSS 127: OEMs and suppliers need to start testing the requirement now to understand where their current technologies fall short and where to focus development.
For more information on how AB Dynamics can support your FMVSS 127 programme, contact us.
In 2024, the European New Car Assessment Programme (Euro NCAP) introduced an update to its Assisted Driving Grading system. In this blog post, Leo Evans, Lead Engineer at AB Dynamics, explores what the update means for the industry, how it aims to enhance consumer understanding, and the impact it will have on the development and assessment of assisted driving systems.
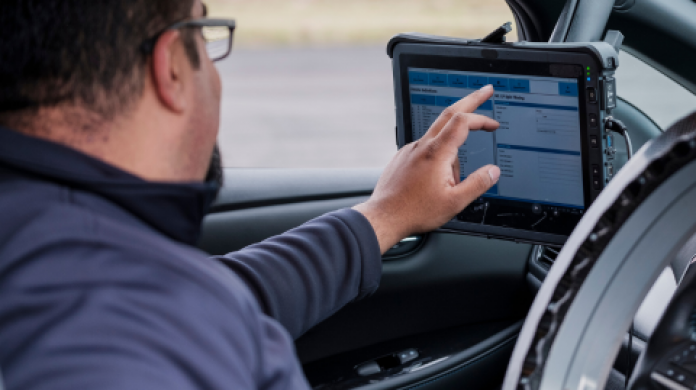
Assessing the performance of assisted driving systems
More and more vehicles are coming to the market with increasingly sophisticated assisted driving systems. The new capabilities of these systems can lead to ambiguity amongst some consumers about the level of assistance they provide. Complaints about some assisted driving systems having misleading names, leading to drivers assuming they are in self-driving or autonomous vehicles when they aren’t are well documented. There are also issues where drivers are opting to disable safety systems due to them being perceived as a nuisance rather than providing assistance.
So how are consumers meant to fairly assess the capabilities and effectiveness of these systems to make informed decisions when purchasing a new vehicle?
Euro NCAP’s new Assisted Driving Grading
Assisted driving refers to level 2 on the SAE driving automation scale. These systems assist the driver to varying degrees but critically the driver remains responsible for all aspects of driving. The more sophisticated level 2 systems combine multiple technologies working in tandem, such as adaptive cruise control and automated lane-keep assist.
Typically, these systems are offered as options and as such aren’t considered in the Euro NCAP star rating. In 2018, Euro NCAP began to study the assisted driving systems available on the market and in 2020 introduced a grading programme based on dedicated test and assessment protocols. The grading system has been updated for 2024 and aims to provide consumers with more information on assisted driving systems and enable them to directly compare their performance with other vehicles on the market.
The updated grading system focuses on two key areas: Assistance Competence, which is the balance between Vehicle Assistance and Driver Engagement, and Safety Backup. The sum of the scores in Assistance Competence and Safety Backup is used in a grading system, similar to the five-star safety rating. Vehicles are currently rated ‘Entry’, ‘Moderate’, ‘Good’ and ‘Very Good’.
The ‘Balance Principal’
The grading system uses what Euro NCAP refer to as the ‘Balance Principal’: The Assistance Competence score is the balance between Vehicle Assistance and Driver Engagement. Driver Engagement includes driver monitoring, driving collaboration, system status and consumer information. Vehicle Assistance includes speed assistance, steering assistance and Adaptive Cruise Control (ACC) performance.
The higher the level of assistance, the more the driver must be engaged by the system. The Euro NCAP Assisted Driving grading places a greater emphasis on keeping the driver engaged and this will be the limiting factor in its scoring. Currently, it is separate to Euro NCAP’s safety rating, but they will be linked in 2026 and fully integrated by 2029. This means that vehicle manufacturers striving for a 5-star rating will need to apply the same level of effort to assisted driving systems as they pay to other safety systems.
The growing quantity and complexity of test scenarios
The aim of the updated Assisted Driving rating system is ultimately to improve road safety, which is unquestionably a good thing. However, to assess assisted driving systems more thoroughly, Euro NCAP has increased the quantity and complexity of test scenarios, making achieving a rating more costly and time-consuming. The latest protocol introduces 40 new on track tests requiring driving robots and ADAS targets, doubling the test effort.
The new test scenarios include the ACC Car-to-Motorcyclist, Collision Avoidance Car-to-Motorcyclist, Car-to-Bicyclist, Car-to-Pedestrian and the Lane Support system – lane change with overtaking vehicle test scenarios. This focus on VRUs (Vulnerable Road Users) will thoroughly challenge assisted driving sensor systems. Motorcyclists, for example, can be difficult to accurately detect and classify when in close proximity to other vehicles, potentially getting lost, or being detected as a single object.
These new scenarios are also more realistic and consider the reality where vehicles may not be centred in the lane-ahead. For motorcyclists there is also the possibility of lane-sharing, bringing additional challenges in establishing whether the lane-ahead is clear. The new scenarios include test cases ranging from 0-100% overlap, varying the potential hit point and better reflecting the real-world challenges. In order to score well, assisted driving systems need to slow down progressively and predictably in the presence of hazardous events to deliver a safe and human-like response.
Increasing test efficiency
Euro NCAP testing is already a time and cost-consuming process, and these additional tests place a greater workload on manufacturers and test houses. To increase efficiency of testing AB Dynamics has enabled the automation of all of the relevant tests within the 2024 Assisted Driving protocol through the configurable test groups in the latest version of our RC software. It allows users to quickly and simply create all the new tests included in Euro NCAP’s Assisted Driving protocol. AB Dynamics enables the coordination of all of the ‘actors’ in a scenario, including robot-controlled vehicles and ADAS targets, allowing the test protocol to be fully defined and executed through a single ecosystem.
Without robotic control of the vehicle, the cut-in scenarios are particularly difficult to orchestrate. Timing when and how the cut-in vehicle should begin its manoeuvre so that it finishes the lane change at precisely the right time relative to the vehicle under test is very complicated. AB Dynamics’ software automatically calculates the trajectories and synchronises the test vehicle and applicable ADAS targets.
Conclusion
Euro NCAP's update to its Assisted Driving grading system marks a significant step forward in enhancing consumer awareness and understanding of the capabilities and limitations of assisted driving technologies. It provides consumers with a clearer picture of how these systems perform and encourages manufacturers to prioritise driver engagement and safety.
The expansion of test scenarios, although demanding for manufacturers and test houses, ensures that vehicles are evaluated under more realistic conditions, leading to better reflection of their performance in real-world situations. The quantity and complexity of testing is only going to increase as assisted driving systems become more advanced. As a result, improving efficiency is increasingly important to all parties in the test industry.
For more information on how AB Dynamics can support your AD programme, contact us.
Over the past decade, the Advanced Driver Assistance Systems (ADAS) market has undergone a rapid transformation. In 2015, 45% of newly registered vehicles worldwide had zero ADAS functionality, in 2025 this is expected to be just 6%. Vehicles have become increasingly equipped with sophisticated technologies to enhance safety and improve the driving experience, and as a result, the demand for robust and realistic testing methods has surged.
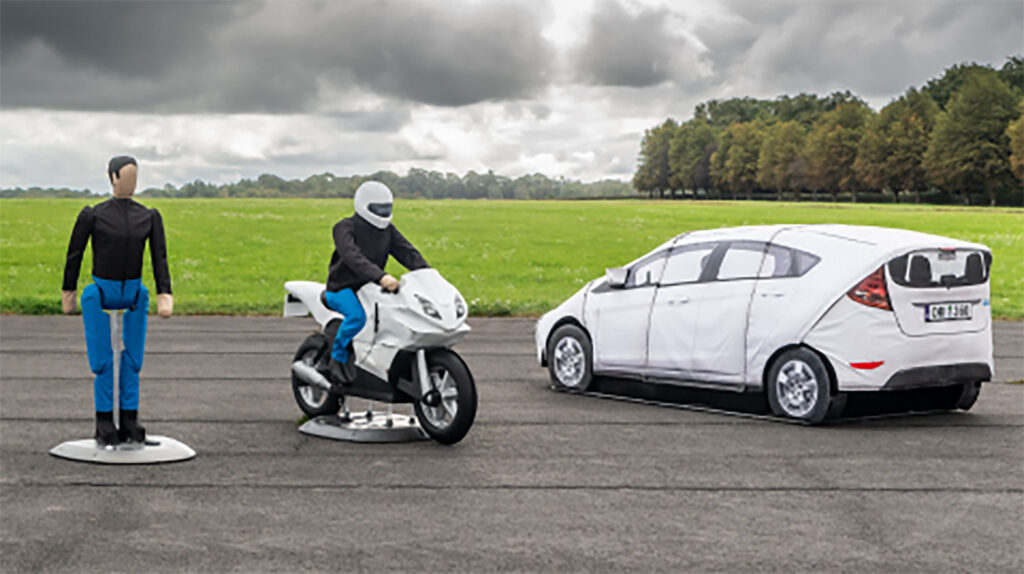
We sat down with Jordan Silberling, General Manager at DRI, AB Dynamics’ California-based sister company and a leading test consultancy specialising in K&C testing, human factors research, ADAS testing and target design. Jordan has been at the forefront of ADAS target development for more than 10 years and helped to create the Soft Car 360, a product that has become synonymous with ADAS testing. Our conversation delves into the challenges of keeping pace with the swift developments in the testing market and highlighting the crucial role realism, robustness and cost-effectiveness plays in creating a successful ADAS target.
Why does the automotive sector need next-gen ADAS targets?
Firstly, as a response to the volume and complexity of ADAS tests, the ADAS market continues to change rapidly. There is a strong desire across the industry to improve vehicle safety and it is clear that advancements in technology are a key enabler to having more effective active safety systems. Vehicles are increasingly being equipped with more sophisticated equipment. They are better than ever at identifying and classifying objects in their environment enabling them to make more informed decisions earlier, which is key to improving safety. As a result, regulatory bodies and consumer bodies are increasing the complexity of tests to challenge these new technologies to continue to drive improved safety. On top of this, vehicle manufacturers want to ensure their systems not only satisfy the testing requirements but also work effectively in the real world too.
Secondly, as an independent test consultancy carrying out hundreds of ADAS tests a year for customers, we experienced first-hand why a new generation of ADAS targets was required. Before we developed our own products, we had to use what was commercially available in the market and we became frustrated with the lack of realism and the damage caused to test vehicles, which was not only costly but also delayed our test programs.
What are your key considerations when designing an ADAS target?
The target must conform to industry standards that dictate particular design elements, such as the dimensions or sensor recognition characteristics. This ensures consistency between targets from different manufactures but restricts the extent of design changes that can be made. They also need to meet certain criteria to be approved for use in official regulatory and consumer testing, such as Euro NCAP.
However, standards conformance is the minimum requirement. Our top priority is to optimise the usability of the target. This ultimately boils down to making the products flexible, durable and cost-effective. We use hard-wearing materials to minimise damage to the target itself and a modular architecture to minimise cost should damage occur.
We also invest heavily in ensuring our targets are as realistic as possible within the constraints of meeting the various standards while not compromising usability. We collaborate with sensor suppliers to better understand how ADAS sensors ‘see’ the world. We also conduct thorough research to help improve the realism of our targets. For example, we have researched pedestrian gait, to ensure the motion of our dummies is representative of humans at a range of speeds. We also commercialised our own specialised scanner device to take radar and lidar measurements of our targets to compare and fine tune them to mimic the signature of the actual objects. It also enables our customers to periodically check that their targets are in conformance with standards.
What about minimising the cost of ADAS testing?
The initial investment in a premium ADAS target might be slightly higher, but the long-term benefits outweigh the costs. Downtime during testing sessions due to target damage or test vehicle damage is a significant factor in overall testing expenses. The last thing you want is your test engineers standing around wasting track time while repairs are being made. As a contracted provider of ADAS testing for the NHTSA (National Highway Traffic Safety Administration), we know this from experience.
As a result, not only do our targets focus on realism but we also prioritise the usability and durability to reduce downtime. Features like interchangeable limbs for pedestrian dummies and ensuring all hard points are minimised contribute to ease of use and minimal disruption during testing, ultimately saving valuable time and resources.
In your opinion, how important are realistic targets?
The primary goal of ADAS testing for most manufacturers is essentially to acquire as much high-quality data as possible. The quality of this data is directly linked to the accuracy of the targets used, which is why DRI’s product development focuses on optimising realism. Compromising on the realism of your ADAS target will result in inaccurate test data. Investing in premium targets ensures not just compliance but provides confidence in the data generated and improves the cost-effectiveness of testing.
Additionally, consider that initial pedestrian ADAS testing required only a static target. Later, dynamic testing was introduced into the regulatory and consumer testing but but currently only articulation of the legs is required. Clearly, this is not fully representative of a human’s gait and could impact the way the vehicle classifies the pedestrian, or indeed the pedestrian’s intent. As a result, I believe articulation of the arms and the head will be a requirement in the near future.
Our Soft Pedestrian 360 target features sophisticated articulation of the knee, hip, shoulder and neck. This provides more control over the gait and allows a greater range of movement than is currently required by regulatory and consumer testing requirements. By making our products as realistic as possible we significantly extend their usability and lifespan.
What role does AB Dynamics play in the development of DRI’s ADAS targets?
A realistic ADAS target is part of the complete test environment required for effective testing. We design targets with the AB Dynamics propulsion system in mind and vice-versa. For example, our Soft Pedestrian 360 and AB Dynamics’ LaunchPad Spin together enable matched motion and speed between the dummy’s legs and the platform’s speed. There are other design criteria to consider too, such as ensuring the targets can match the speed capabilities of the platforms and how the combination of products impacts the radar signature. Ultimately, our combined solution ensures that the dummy motion can be integrated into the heart of the scenario, simplifying setup, and guaranteeing realism.
What industry trends are shaping the future development of ADAS targets?
Intent will be key going forward. That is, systems will begin trying to determine the intent of a pedestrian, for example, by reading the person's body language. This is something we do as humans instinctively. If you see somebody stopped at the roadside looking both ways you know they intend to cross the road and you can adjust your driving as a result. AI-trained systems and real-time image and video processing are learning to look for these cues. As the industry evolves, the integration of vision software becomes crucial in classifying and tracking objects. Pedestrian targets will need to be able to mimic these behaviours to thoroughly test these systems.
We achieve this in the Soft Pedestrian 360 through sophisticated limb articulation and its modular architecture, which enables the standard arm to be switched with an arm holding a mobile phone, for example. The LaunchPad Spin, the platform that the target is moved by, provides turn-on-the-spot mobility to replicate sudden changes in direction or intent.
Key Takeaways:
- Rapid evolution of ADAS market: The ADAS market has transformed rapidly, with a significant growth in vehicles equipped with increasingly advanced ADAS functionality. This is driving a surge in demand for more sophisticated and realistic ADAS targets.
- Importance of realism in ADAS testing: DRI emphasises the pivotal role of realism in ADAS testing. Premium ADAS targets, such as the Soft Pedestrian 360, offer sophisticated articulation to ensure a realistic testing environment and future-proof testing.
- Making testing more cost-effective: Prioritising usability and durability minimises downtime during testing, saving valuable time and resources.
- Emerging trends in ADAS testing: DRI anticipates a shift towards a focus on interpreting human intent in ADAS testing. ADAS targets must emulate these behaviours to effectively test and validate image and video processing systems.
For more information on DRI’s market leading ADAS targets, visit their website here or watch AB Dynamics’ latest webinar “A complete solution for NCAP motorcycle scenario testing”, where Jordan Silberling provides insights into DRI’s Soft Motorcycle 360 target.
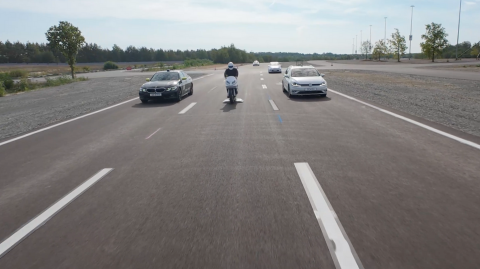
As the automotive industry continues to shift towards more advanced driver assistance and automated driving, our Business Director of Track Test Systems, Dr. Andrew Pick explores the future challenges, advancements, and direction of testing methodologies.
How has the landscape of automotive testing changed over the past decade?
Over the last decade, we've witnessed a significant transformation in automotive testing. Driver assistance systems have now filtered down from premium vehicles to becoming a standard feature in every new vehicle thanks to changes in legislation to improve safety. This shift has significantly increased the requirement for ADAS testing and places a higher burden on OEMs, test houses and test equipment. As a result, we have focussed our product development programmes to meet this changing demand and help improve testing efficiency.
What challenges do test engineers face with the rise of driver assistance systems?
While regulatory and consumer testing typically involves only the vehicle under test and a single ADAS target, real-world scenarios are often much more complex. For example, traffic can cause distractions and obscure the driver’s, and sensor’s, view of an impending collision. Even if legislation doesn’t necessitate more complex scenarios in the future, the demand from consumers for a better driving experience will. As such, the testing of driver assistance systems will require an increasingly accurate representation of real-world scenarios. We are actively addressing this by incorporating greater realism into our ADAS targets, introducing additional targets, and enabling more complex scenarios to take place.
How does AB Dynamics envision the future of testing for driver assistance systems?
We are already seeing a shift towards more realistic and complex testing scenarios. For example, Euro NCAP's cut-out scenario, focusing on adaptive cruise control in following traffic, highlights the need to consider the effects of multiple vehicles. On top of this, increasing levels of automated driving also necessitate more complex testing.
How will automated driving impact testing?
ADAS technologies are not infallible, but they don't need to be. As the name suggests, they are there to assist the driver and their purpose is to reduce the probability of collisions resulting from driver errors. However, as we move towards automated driving functions, which assume responsibility for driving tasks, the robustness of these systems becomes absolutely crucial, and testing is a critical part of validating this. Simulation will play an increasing role in subjecting these systems to the almost limitless possibilities that can occur on our roads but ultimately these simulated tests will need to be correlated in the real world. Testing will need to encompass every conceivable scenario, driving an increase in the volume of testing as automation becomes more prevalent.
How will testing requirements for automated driving differ from current practices?
Automated driving functions demand new testing methods and tracks. For example, we anticipate that the current single-run approach to testing will need to be replaced by a more efficient fluid solution. Imagine a swarm of vehicles continuously repositioning to perform a multitude of uninterrupted scenarios over hundreds of kilometres on a looped track. We are developing new communication technologies as well as scenario planning and execution tools to enable this type of testing. It will require proving grounds to develop new facilities to allow continuous running on multi-lane highways to meet this type of testing.
How is AB Dynamics preparing for the future of automated driving testing?
We are ready to embrace the future challenges in automated driving testing. As the industry works towards providing safe and affordable automated driving, we are committed to delivering cutting-edge test solutions. Our focus is on adapting to new testing methodologies, developing innovative products, and contributing to the evolution of the automotive testing landscape.
Key takeaways:
- Over the last decade, the need for increased ADAS testing has placed a higher burden on OEMs, test houses, and test equipment.
- Real-world scenarios are often more complex than regulatory and consumer testing, which typically involves only the vehicle under test and a single ADAS target.
- AB Dynamics envisions a shift towards more realistic and complex testing scenarios. Increasing levels of automated driving will necessitate more complex testing.
- Automated driving functions demand new testing methods and tracks. AB Dynamics anticipates that the current single-run approach to testing will need to be replaced by a more efficient fluid solution.
For more information on how AB Dynamics can support your ADAS testing programme visit click here or contact us at info@abdynamics.com.
In part one of this blog series, the benefits of using objective test data for the development of complex hybrid braking systems were introduced. In this second part, Allan Johnstone, Principal Project Engineer at AB Dynamics uses a working example to detail the methodology.
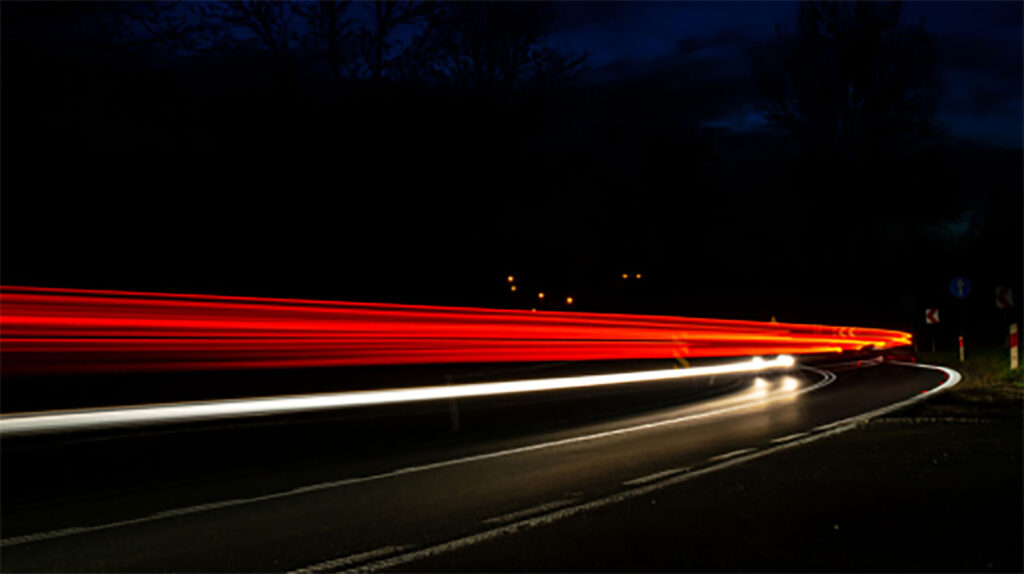
When the regenerative brake system on an electrified vehicle reaches its limit of deceleration the mechanical foundation brake needs to be blended in to make up the shortfall. Typically, this happens at a deceleration rate of >3m/s2 or when the vehicle’s speed approaches 0 km/h because the braking torque from the electric motor drops off. In these scenarios, where the systems are being blended, brake feel is critical because often the driver can experience varying levels of deceleration for a given demand. This can be disconcerting and result in the driver needing to modulate the brake pedal input, which can exasperate the issue.
Brake feel analysis using brake robots
For the first time, this type of situation can now be objectively tested using our brake feel analysis solution, which incorporates brake robots fitted to the subject vehicle together with control and analysis software. In the following example, the test vehicle is a popular European EV and the test simulated the vehicle coming to a stop approaching a set of traffic lights. This involved an AB Dynamics RBR 600 model brake robot applying the brake to a specific position and holding the pedal constant, until the vehicle came to rest.
From this type of stop, the contribution of the regenerative and the foundation brake can be separated out and visualised (Figure 1).
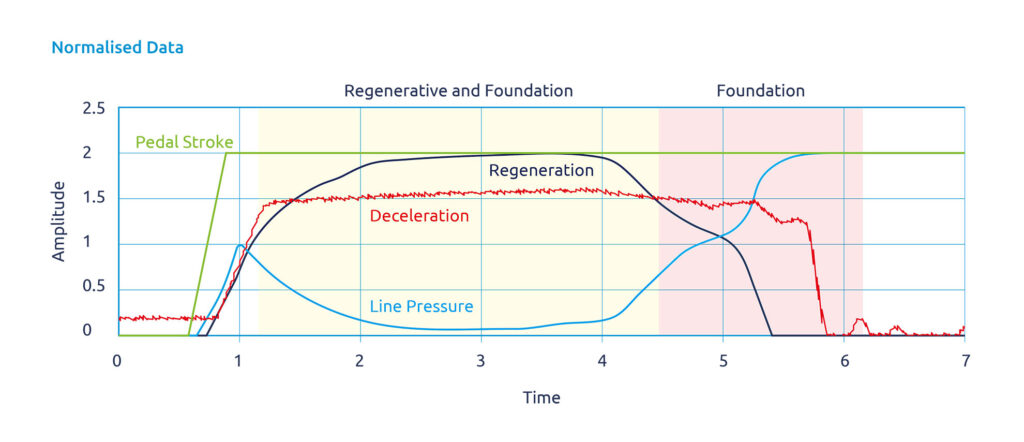
Figure 1 Visualisation of EV regenerative and foundation brake blending
In Figure 1, the deceleration begins to drop after four seconds. This is generally viewed as a negative characteristic because the driver is required to compensate for the system’s shortfalls by increasing pedal input.
The rating for this type of stop is a relatively low value, which is expected from this level of deceleration reduction during a stop.
This demonstrates that the vehicle has poor brake feel (5.5 on the brake rating index, see part 1) in this scenario as the deceleration reduces despite a constant brake demand. To compensate, the driver must respond by applying more brake stroke. This type of brake characteristic reduces the driver’s level of confidence in the braking system and might even increase the likelihood of low-speed collisions as the driver underestimates the pedal stroke required to stop in time. This is a common issue with EVs as the regenerative braking torque reduces at lower speeds so the foundation brake needs to compensate. If the system fails to do this adequately it will require input from the driver.
Regenerative braking systems are significantly more complex than traditional setups. The development of these systems is still evolving as the technology advances. To accelerate the development, engineers would benefit greatly from a tool that can test, analyse, and evaluate them accurately and repeatably providing valuable objective data.
The AB Dynamics brake robots that are used as part of the brake feel analysis solution provide a level of control to the brake pedal that is beyond that of any driver, with levels of precision that have not been possible before. The repeatable inputs from the brake robots enable the braking system’s performance to be accurately measured, taking into account a reduction in the battery state of charge or a modification in the blending algorithm.
Our solution bridges the gap between objective and subjective evaluation, allowing the user to quickly understand the subjective impact of the braking system providing a visualisation of each braking characteristic and a subjective score. Importantly, this information provides quantitative information that can be shared within and across teams, providing the basis for objective decision-making.
This information will be critical in ensuring that brake feel and performance are to a level expected by consumers, leading to better satisfaction and reduced warranty issues.
Key takeaways
- Hybrid braking systems are complex and challenging to optimise, as they depend on multiple variables such as battery state, friction level, and driving conditions.
- AB Dynamics has developed a solution to objectively test and analyse the brake feel of hybrid vehicles.
- This solution enables engineers to optimise the brake controller, benchmark competitor systems, and validate brake system performance using objective data and subjective feedback.
- A working example of the solution applied to a popular European EV, demonstrates how the contribution of the regenerative and the foundation brake can be separated out and visualised, and how the brake feel rating can be calculated and interpreted.
For more information on our brake development solutions click here or to discuss your programme requirements contact us at info@abdynamics.com
Electric vehicles (EVs) are becoming more popular as they offer many benefits such as lower emissions and reduced fuel costs. However, one of the key challenges that EV manufacturers face is how to ensure that the brake system of their vehicles provides a consistent and comfortable feel for drivers. This is especially important for hybrid systems that combine mechanical and regenerative braking, which can vary depending on the battery state, the friction level, and the driving conditions.
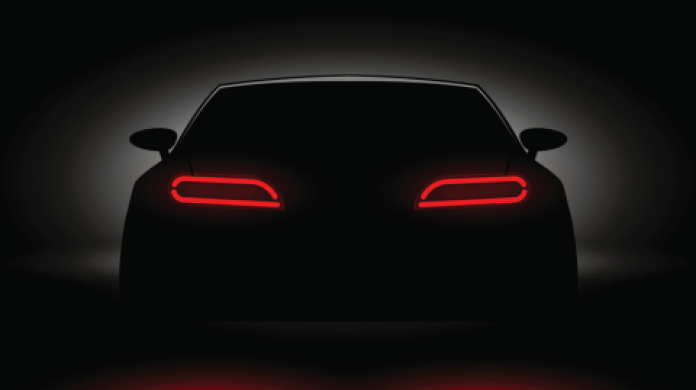
In this blog post, Allan Johnstone, Principal Project Engineer at AB Dynamics discusses a novel solution developed by AB Dynamics that enables objective data analysis of the brake feel of hybrid systems and explains how brake robots, control and analysis software, and a brake rating index can help engineers to optimise the brake controller, benchmark competitor systems, and validate brake system performance.
Winning the EV revolution
The winners of the EV revolution will be those manufacturers that remove, or reduce as much as possible, the barriers to adoption. A fundamental challenge for EV manufacturers has been the integration of complex hybrid braking systems, combining the traditional mechanical foundation brake and the electric regenerative system. Ensuring the brake system feels consistent to what consumers have already become accustomed to is a critical barrier to overcome.
The challenge for engineers is to seamlessly blend the two systems together while maximising regenerative braking to recharge the battery to maximise vehicle range. This is most commonly achieved by using a brake-by-wire system, where the pedal characteristic, stroke and load are provided by a pedal simulator element and the braking demand by a stroke sensor. The brake controller blends the two systems to produce the required deceleration requested by the driver.
Commonly in EVs the driver experiences varying levels of deceleration for the same braking demand, making the brake feeling unpredictable at best, or at worst unsafe, which can lead to costly recalls. This is often caused by the variables within the system, such as the state of charge of the battery and the friction level between disc and pad, which changes with temperature, moisture levels and wear.
Traditionally, brake feel has relied solely on the subjective assessment of brake engineers. In order to change this and to prevent poor brake feel it is key to inject thorough objective test data into the development process. This enables engineers to analyse the braking system at all variable points, optimise the brake controller, assess individual components, accurately benchmark competitor systems, and support subjective feedback that can often be misinterpreted.
AB Dynamics has developed what it believes to be the industry’s first objective brake feel assessment solution that uses brake robots fitted to the subject vehicle together with control and analysis software. Our solution enables the objective testing of a vehicle’s braking system and provides an automated analysis upon completion of the testing. The software uses an algorithm to assess the vehicle’s brake feel based on the SAE brake rating index.

Brake rating index
The data used for the analysis is acquired through our brake robots, which are specifically designed to provide accurate and repeatable applications of the brake pedal. They are widely used by the automotive industry for applications such as testing of ADAS technologies, durability and misuse testing.
The control parameter can be pedal stroke, pedal load, a level of deceleration or a mixture of the three. The result is quantifiable measurements of the vehicle’s brake system across various conditions and vehicle speeds. Our solution automatically assesses a wide range of aspects including stroke effectiveness, load effectiveness, booster reaction and low and high-speed build-up to determine the three key areas that contribute to brake feel: system stiffness, system response and friction characteristics.
AB Dynamics has worked with expert brake system evaluators to convert this objective data into a usable subjective score to provide an instant judgement of overall brake feel. This gives engineers more confidence in assessing and signing off the brake system by knowing that their evaluation is supported by objective data.
Critically, the data produced by our brake feel analysis system also enables the development of an accurate digital model of the braking system for incorporation into vehicle models and virtual validation. The brake feel tool can also be integrated into a Hardware-In-the-Loop (HIL) test rig. This enables the control of the blended braking system to be matured well ahead of a physical prototype vehicle, saving significant time and money.
Key takeaways:
- Brake feel is a critical factor for EV adoption, as consumers expect a consistent and comfortable braking experience.
- Hybrid braking systems are complex and challenging to optimise, as they depend on multiple variables such as battery state, friction level, and driving conditions.
- AB Dynamics has developed a unique solution that enables objective data analysis of the brake feel of hybrid systems, using brake robots, control and analysis software, and brake rating index.
In the next part of this blog series, a working example of AB Dynamics’ assessment tool will be presented. In the meantime, if you want to learn more about our solution and how it can help you improve your EV brake feel, contact us at info@abdynamics.com
In a recent announcement, the US federal government's National Highway Traffic Safety Administration (NHTSA) has proposed a ground-breaking regulation that could have a transformative impact on road safety. NHTSA is advocating for all new passenger cars and light trucks sold in the United States to be equipped with automatic emergency braking (AEB) systems.
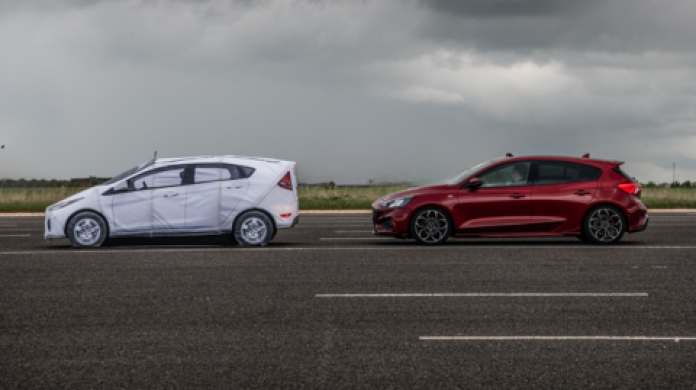
This directive carries immense significance for both the automotive industry and the safety of motorists and pedestrians. In our latest blog post, David Marquette, Business Development Director at AB Dynamics North America, delves into the details of the proposed mandate, its potential implications, and the role of companies in supporting its implementation.
The Power of Automatic Emergency Braking (AEB)
Automatic emergency braking (AEB) is a safety technology designed to assist drivers in mitigating or avoiding collisions. By employing sensors, cameras, and sophisticated algorithms, AEB systems detect potential hazards and automatically apply the brakes to prevent or reduce the severity of accidents. This technology has proven to be highly effective in preventing injuries and saving lives by providing an additional layer of protection and response capabilities.
For example, research conducted by the European Commission indicated that vehicles equipped with AEB technology experienced approximately 38% fewer rear-end crashes. Additionally, the same study highlighted that AEB systems with pedestrian detection reduced pedestrian fatalities by approximately 27%.
NHTSA's Proposal
NHTSA's primary mission is to ensure road safety by establishing and enforcing vehicle performance standards and regulations. They work to improve vehicle and road safety, reduce accidents, and promote innovations in transportation technologies. NHTSA also plays a crucial role in shaping policies and initiatives aimed at protecting motorists and pedestrians across the US. Its latest proposal to make AEB systems mandatory in all new passenger cars and light trucks is a significant step towards enhancing road safety.
NHTSA estimates the technology could reduce injuries by at least 24,000 annually and save over 360 lives per year; however, it's important to note that this appears to be a conservative estimate based on over 70,000 car pedestrian accidents annually in the US where 9% result in death. The proposal will now go through the process of consultation and review. This allows for discussions among stakeholders to address concerns, fine-tune regulations and importantly allows the needed time for the automotive industry to ensure their vehicles and technology are ready for the forth coming rule making.
Lessons from the EU
The European Union (EU) has already taken strides in implementing AEB technology. Since 2022, AEB has been mandatory on all new model passenger vehicles introduced in the EU and by 2024, every new car sold in the EU will need to be fitted with this technology. This serves as a valuable precedent, demonstrating the successful integration of AEB systems and their positive impact on road safety. The EU's experience can provide insights and best practices for the US as it moves towards implementing similar regulations.
Supporting implementation
Companies like AB Dynamics currently play a vital role in supporting the implementation of AEB systems and ensuring their effectiveness. We have developed advanced testing, simulation, and validation solutions that enable automakers to develop and test the performance of AEB systems. For example, the Guided Soft Target (GST) system, consisting of the GST platform and Soft Car 360, is one of the core technologies used to evaluate and enhance the capabilities of AEB systems. By simulating real-world scenarios and providing a controlled testing environment, these technologies enable automakers to validate the functionality, reliability, and safety of AEB systems before they are deployed in vehicles.
Key takeaways
NHTSA's proposed regulation mandating automatic emergency braking (AEB) systems in all new passenger cars and light trucks sold in the US is a significant stride towards a safer future on the roads.
- By leveraging the power of safety technologies, such as AEB, there is opportunity to prevent accidents, mitigate the impact of collisions, and save lives.
- Implementation may take time due to the consultation and review processes; however, lessons from the EU's successful AEB adoption can guide the US on its journey.
- Companies like AB Dynamics, with our testing, simulation, and validation solutions, will continue to play a crucial role in supporting the automotive industry in integrating and optimising AEB systems.
- NHTSA estimates AEB technology could reduce injuries by at least 24,000 annually and save over 360 lives per year, but data suggests this is a conservative number.
For more information on how AB Dynamics can support your AEB systems testing requirements, contact us at info@abdynamics.com
This year AB Dynamics and its sister company Dynamic Research Inc. (DRI) celebrate the 10th anniversary of the first sale of the Guided Soft Target (GST) surrogate vehicle target system. In this blog, Joseph Kelly, Chief Engineer at DRI, explains how the GST has set the global standard for 3D vehicle targets and has helped to revolutionise the testing and development of lifesaving ADAS technologies.
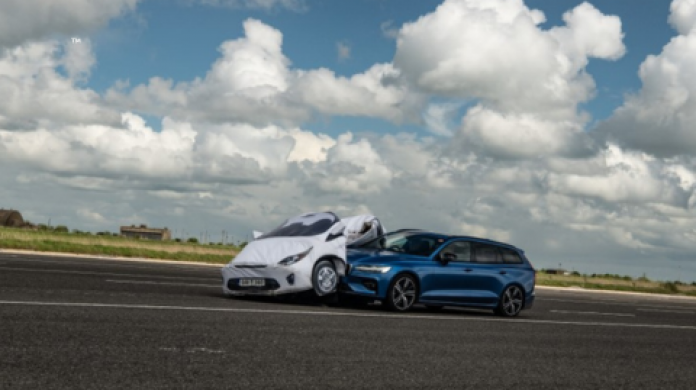
The GST test system consists of the Soft Car 360, an impactable dummy vehicle target attached to a low-profile robotic platform designed to be run over by vehicles. In this article, we will be looking at the origins of the GST and the industry trends that have shaped its design.
The history of the GST
The GST’s story starts in 2007 when crash avoidance technologies, such as Automatic Emergency Braking (AEB), were still in their infancy and so too were the systems to test them. A variety of targets, ranging from simple radar reflectors to partial vehicle representations (both static and dynamic), were developed to aid in the evaluation of rear end collision avoidance and mitigation systems, but these had limitations restricting approach speeds and angles, as well as lateral offsets. Additionally, some of the dynamic systems required the presence of other vehicles to tow the targets, or suspend them from above, which could sometimes adversely affect the performance of the vehicles under test.
It was at this time that DRI collaborated with NHTSA (National Highway Traffic Safety Administration) on the ACAT (Advanced Crash Avoidance Technologies) project, together with Honda. The project aimed to develop practical methods for evaluating the effectiveness of emerging ADAS technologies. A key phase of the project was to establish the test requirements in order to conduct full-scale testing of the technologies.
The project identified three key vehicle-to-vehicle scenarios that would need to be tested, which were head on, rear end and crossing paths.
These tests necessitated a dynamic solution that was strikeable from multiple angles that:
- Did not damage the vehicle during test,
- Did not present a safety risk to test personnel,
- Was easily reconfigurable and enabled close coordination of vehicles with regard to conflict conditions such as closing speed and angle, and
- Could easily be reset after impact for further testing.
The solution: the GST system. Through this project, DRI became fundamental in finding ways to help the industry test and develop first-generation collision avoidance systems that have since been developed into today’s technologies.
The initial development of what would become recognisable as the GST system used a simple vehicle target constructed from foam, fitted to a first-generation version of the GST platform, which was affectionately known internally as the ‘Turtle’. It was the first self-propelled dummy vehicle target that could be safely run over, providing unrivalled testing flexibility. Designed initially for detection by lidar, the system’s visual representation of a vehicle and its radar reflectivity were less relevant. The entire system was designed and manufactured in-house at DRI, including the platform’s navigation and control system.
DRI recognised that the appearance and durability of the target needed to be improved to be useful to manufacturers using camera and radar systems and this formed the core development path for the following few years. A project with IIHS (Insurance Institute for Highway Safety) in 2011 and feedback from other industry experts identified a demand for stable radar reflectivity, which resulted in the introduction of a new reflective material for the Soft Car 360. Other developments included enclosing the foam skins in vinyl fabric “pillowcases”, which allowed the application of photorealistic graphics and increased durability and realism. The result was a first-generation version of the Soft Car 360 that we know and recognise today.
DRI’s involvement in these industry projects led to the development of equipment that is now in use globally to thoroughly test ADAS technologies. Worldwide adoption of standardised tests that rely on this equipment is helping to provide safety ratings of new vehicles to educate consumers and improve road safety.
In 2012 DRI developed what became the first commercially available GST that incorporated all the various features to make it representative to a variety of sensor systems. Later that year, DRI began its partnership with AB Dynamics to further develop the product and the first unit was delivered to an Asian OEM in 2013.
This partnership allowed customers to experience AB Dynamics’ tried and tested control hardware and software from the steering and pedal robots in a driverless platform. It also allowed for seamless synchronisation between robots thanks to AB Dynamics’ patented Synchro software.
In 2014, DRI developed the second generation GST in collaboration with NHTSA. This project involved reducing the radar reflectivity of the platform and increasing the acceleration and top speed, to cater for the growing variety of tests being carried out. There was also a heavy-duty version developed for trucks. In 2018, AB Dynamics introduced the MK2 GST platform, bringing improvements to the market, such as a lower overall profile, 100 km/h top speed and improved path following.
The collaboration between AB Dynamics and DRI proved to be a great success resulting in the GST’s approval for use by Euro NCAP and NHTSA as its Global Vehicle Target in 2018. The relationship further strengthened when DRI joined the AB Dynamics group through an acquisition in 2019.
In 2020, during the COVID-19 pandemic, AB Dynamics introduced the GST 120, the highest top speed GVT on the market. This was an incredible engineering achievement as although a 20 km/h increase in speed doesn’t seem much, an astounding 70% increase in power is required. Alongside its increased top speed, an Anti-lock Braking System (ABS) was also introduced, which later became standard on all GST products.
Since its initial introduction the GST has been continually developed, particularly to improve its realism in line with the increasing sophistication of ADAS perception and classification technologies, and the Soft Car 360 is currently in its seventh revision.
Industry drivers and challenges
When the GST was first introduced ten years ago, advanced crash avoidance technologies were usually found on higher-end luxury vehicles. Thanks, in part, to the ACAT projects these technologies were becoming more mainstream and Volvo was the first OEM to fit AEB as standard on all new models in 2014. The continued development of these technologies and an increased focus on safety regulations has driven the mass adoption of collision avoidance and mitigation systems.
One of the most used sensor systems is radar. It scans the world very efficiently but often lacks definition and is limited in providing data on verticality, which would be useful in correctly classifying objects. Increasing the resolution of radar systems is a key area for development for OEMs. The GST system has been future-proofed in this respect as the GST platform has been designed to minimise radar reflectivity, whilst the Soft Car 360 has been optimised from top to bottom to reflect radar realistically.
Although very efficient in the way it transmits and receives data, radar does have its limitations. As a result, OEMs are now moving towards sensor fusion, combining a variety of sensors to more accurately perceive the world ahead. For example, a camera and radar system sense the world in disparate but complementary ways leading to a much better perception system than would be possible from a single type of sensor.
As these technologies have matured and adoption has increased, the challenge for the industry has shifted from simply avoiding and mitigating a potential crash to them being more usable on the road and not issuing false positives. This is critical in translating these technologies into real world road safety improvements.
To achieve this the vehicle must correctly discern what it can and can’t ‘drive into’. A good example of this problem are steel trench plates, used for covering up holes or trenches in the road during road works. They are large and reflective to a radar system, just like a car, so they could be mistakenly perceived as a parked car, as a result, vehicles could apply full braking as they approach. This is where a combination of sensor systems should be able to correctly identify the object and make the correct decision to not intervene.
The future of the GST
These industry trends have driven the development path of the GST system. The Soft Car 360 has been developed in collaboration with industry partners, including sensor manufacturers and OEMs, through workshops coordinated by Euro NCAP, NHTSA, and IIHS. This collaboration has been critical in improving the realism of the target and understanding how it is perceived by the many different sensor technologies used on a vehicle.
Additionally, the quantity and complexity of ADAS testing is expected to continue to grow exponentially and so too are the tools used to test these systems. The hatchback version of the GST has been approved for use in NCAP tests since 2018 but there is a range of vehicle targets available, including a micro, sedan and estate version. This range will continue to expand to provide customers with the variety required to thoroughly test a vehicle’s sensor system.
One of the next big steps in active collision avoidance technologies is likely to come from increased connectivity. The ability for a vehicle to communicate with infrastructure and other vehicles around it increases awareness of potential dangers and the time to react. The integration of connectivity, or V2X (Vehicle-to-Everything), will significantly impact the testing landscape. AB Dynamics is participating in the SECUR project (Safety Enhancement through Connected Users on the Road), which aims to create a coherent proposal for V2X testing and assessment protocols for Euro NCAP. AB Dynamics’ key input into the project is to help define a specification for connected targets to support V2X testing in the future.
The GST timeline:
- 2007 – DRI starts collaboration with Honda and NHTSA on the Advanced Crash Avoidance Technologies (ACAT) project.
- 2008 – DRI develops the Low-Profile Robotic Vehicle (LPRV) ‘Turtle’, an early version of what would become the GST platform, and a simple Soft Car 360.
- 2010 – DRI continues development of the Soft Car 360, integrating a multi-panel construction design.
- 2012 – DRI signs collaborative agreement with AB Dynamics.
- 2013 – First GST delivered to customer.
- 2014-2015 – The second generation GST is developed for NHTSA, including heavy duty truck compatibility.
- 2018 – The GST is approved as the official Global Vehicle Target (GVT) by NHTSA, IIHS and Euro NCAP. The GST MK2 platform introduced with various improvements, higher top speed (100 km/h) and lower overall height.
- 2019 – DRI acquired by AB Dynamics.
- 2020 – AB Dynamics becomes a partner in the SECUR project featuring the GST system. The GST 120 introduced, the fastest GVT in the market, with a top speed limited to 120 km/h. Also introducing improved path following at high speeds as well as ABS to the GST line up.
- 2022 – GST 120 and Soft Car 360 were officially approved by Euro NCAP under Technical Bulletin 29.
- 2023 – It is the ten-year anniversary of the delivery of the first GST. GST and V2X demonstration for the SECUR project.
For more information on the GST test system or to arrange a demo, contact us at info@abdynamics.com