In this guest interview, we speak to Raoul Popescu-Ghimis, Chief Executive Officer of RACE Software, a software package for the development of suspension systems. We discuss the challenges of modern suspension design, the role of simulation in overcoming them and how simulation combines with real-word data to create high-quality digital models. Integrating precise data from a kinematics and compliance (K&C) rig into simulation creates a powerful feedback loop where physical testing informs simulation and vice versa.
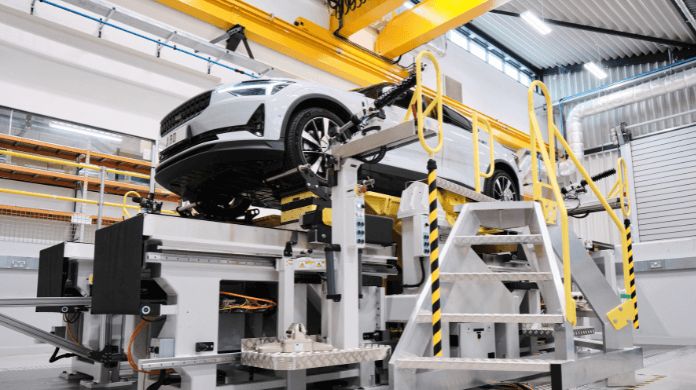
Can you tell us a little bit about your background?
I worked for companies such as Multimatic, HORIBA MIRA, and Jaguar Land Rover, where I developed vehicle chassis and vehicle dynamics for both the automotive and motorsport sectors. With over a decade of experience in the field, and recognising the limitations of traditional vehicle development tools, I teamed up with our CTO, Damien Maher, to bring RACE (Rapid Axle Concept Evolution) Software to life.
What does RACE Software do?
RACE Software specialises in suspension and chassis design, offering multibody dynamics simulation (MBS) solutions. Our platform integrates model building, parameterisation, post-processing, data storage, and report generation into one system. It enables users to complete K&C analysis for an axle quickly. By combining complex physical data with advanced simulation algorithms, our platform allows engineers to predict vehicle performance, significantly accelerating the design process while ensuring precision and cost-effectiveness.
What are the core challenges of suspension design and how does simulation help to overcome it?
Suspension design is inherently complex as it requires balancing multiple, often conflicting factors. Engineers must optimise for ride comfort, handling performance, durability, and safety, while also considering vehicle weight, cost, and environmental impact. One of the key challenges is predicting how the suspension system will perform under a wide range of real-world conditions, including different road surfaces, loads, and driver behaviours. Traditional methods, which involve building physical prototypes and conducting extensive testing, are both time-consuming and expensive.
Simulation helps to address these challenges by enabling engineers to create virtual models of suspension systems, allowing for rapid testing and iteration. By simulating real-world scenarios, engineers can explore different design alternatives and fine-tune suspension performance before any physical prototypes are made. This not only speeds up the development process but also significantly reduces costs associated with physical testing. Furthermore, simulation provides insights that are often difficult, if not impossible, to obtain through physical prototypes, enabling more precise optimisations and improving the final product's overall performance. This approach streamlines the development cycle, enhances innovation, and ensures a higher-quality suspension system.
Could you explain how simulation tools interact with physical data, and why this combination is crucial for optimising suspension design?
By integrating simulation tools with real-world data obtained from physical testing equipment provides valuable insights into how suspension and chassis systems behave under different loads and conditions. It creates highly accurate virtual representations of suspension systems that reflect real-world behaviours.
This integration of physical data and virtual simulation is essential for efficiently optimising suspension design, as it allows engineers to validate their designs early in the development process. Ensuring that the virtual model aligns with real-world performance significantly reduces the risk of costly errors during production. The ability to conduct numerous virtual tests in a fraction of the time required for physical testing allows for greater innovation and engineering excellence in design. By leveraging real-world data, engineers can make informed design decisions, enhance accuracy, and ultimately improve the performance of suspension systems. This combined methodology not only streamlines the design process but also leads to better overall outcomes for both manufacturers and customers.
One of the biggest industry trends at the moment is the move towards electric vehicles. How does this impact suspension design or characteristics designers are targeting?
The current trends towards electric vehicles (EVs) are significantly reshaping suspension design and the characteristics that engineers prioritise. One of the primary impacts of EVs is the increase in weight due to the heavy battery packs and also the shift in weight distribution, resulting in a lower centre of gravity. This necessitates the development of suspension systems that enhance stability and handling while accommodating the unique weight dynamics of electric drivetrains.
Additionally, the quiet and vibration-free operation of EVs places a greater emphasis on ride comfort and noise, vibration, and harshness (NHV) management. Designers are increasingly focused on creating suspension systems and bushings that not only effectively absorb road irregularities, but also ensure a smooth ride experience for passengers.
How important is it to have access to real-world data to support and improve simulation tools?
Working with AB Dynamics is essential for us at RACE Software. Its expertise in providing high-quality, real-world data through the SPMM Plus, is invaluable in refining our simulation models. It allows our simulations to closely mirror real-world performance, creating a powerful feedback loop where physical testing informs simulation and vice versa.
By integrating precise data on vehicle dynamics and suspension performance, we ensure that our simulation tools do not operate in isolation but are grounded in practical performance metrics to enhance the accuracy and reliability of our models.
Our work with AB Dynamics helps to improve the performance of suspension designs, providing greater value to clients and ensuring that our solutions meet the evolving needs of the automotive and motorsport industry.
Can you provide an example where physical data from a K&C machine has been used to improve the correlation of the simulated results?
An automotive manufacturer provided us with a K&C test report and suspension data for a passenger vehicle. Using this data, including suspension geometry and system stiffnesses, we built a virtual model that accurately replicated the suspension system. Where certain stiffnesses were not directly measured, we utilised the K&C report to reverse-engineer these values and adjust the model. By integrating the physical data from the K&C test into the virtual model, we were able to fine-tune critical parameters, resulting in a close match between the simulation and actual suspension performance. This improved the correlation and accuracy, allowing the client to make more confident design decisions.
After the virtual model was correlated, numerous virtual K&C simulations were run to develop the suspension system to meet the new set targets. Once the final design was achieved, a physical prototype was built and validated on a K&C machine before entering production. This process not only improved the workflow but also reduced development time and costs, enabling the client to achieve a suspension system that exceeded their performance targets.
Key takeaways:
- Challenges in suspension design: Modern suspension design involves balancing multiple factors such as ride comfort, handling performance, durability, safety, vehicle weight, cost, and environmental impact.
- Role of simulation: Simulation helps overcome the challenges of suspension design by enabling rapid testing and iteration of virtual models, reducing the need for physical prototypes and extensive testing.
- Using real-world data to improve the quality of simulations: High-quality, real-world data from advanced testing equipment like K&C machines can be used to correlate and improve the accuracy of simulation tools, such as RACE software.
- Integration of physical data: By incorporating real-world data into simulation models, RACE Software ensures accurate virtual representations of suspension systems, improving the reliability and performance of the designs.
- Impact of electric vehicles: The shift towards EVs is reshaping suspension design, with a focus on handling increased weight, lower centre of gravity, and enhancing ride comfort and NVH management.
- Importance of real-world data: Using real-world data to validate designs early in the development process, reduces the risk of costly errors and enhances the accuracy of simulation models.
To learn how AB Dynamics and RACE Software are shaping the future of suspension development, contact us.
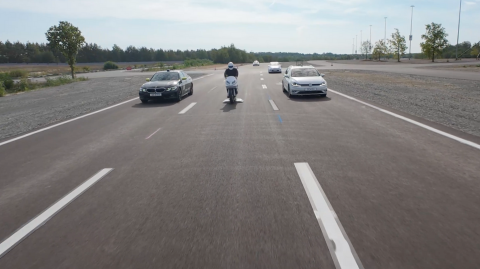
As the automotive industry continues to shift towards more advanced driver assistance and automated driving, our Business Director of Track Test Systems, Dr. Andrew Pick explores the future challenges, advancements, and direction of testing methodologies.
How has the landscape of automotive testing changed over the past decade?
Over the last decade, we've witnessed a significant transformation in automotive testing. Driver assistance systems have now filtered down from premium vehicles to becoming a standard feature in every new vehicle thanks to changes in legislation to improve safety. This shift has significantly increased the requirement for ADAS testing and places a higher burden on OEMs, test houses and test equipment. As a result, we have focussed our product development programmes to meet this changing demand and help improve testing efficiency.
What challenges do test engineers face with the rise of driver assistance systems?
While regulatory and consumer testing typically involves only the vehicle under test and a single ADAS target, real-world scenarios are often much more complex. For example, traffic can cause distractions and obscure the driver’s, and sensor’s, view of an impending collision. Even if legislation doesn’t necessitate more complex scenarios in the future, the demand from consumers for a better driving experience will. As such, the testing of driver assistance systems will require an increasingly accurate representation of real-world scenarios. We are actively addressing this by incorporating greater realism into our ADAS targets, introducing additional targets, and enabling more complex scenarios to take place.
How does AB Dynamics envision the future of testing for driver assistance systems?
We are already seeing a shift towards more realistic and complex testing scenarios. For example, Euro NCAP's cut-out scenario, focusing on adaptive cruise control in following traffic, highlights the need to consider the effects of multiple vehicles. On top of this, increasing levels of automated driving also necessitate more complex testing.
How will automated driving impact testing?
ADAS technologies are not infallible, but they don't need to be. As the name suggests, they are there to assist the driver and their purpose is to reduce the probability of collisions resulting from driver errors. However, as we move towards automated driving functions, which assume responsibility for driving tasks, the robustness of these systems becomes absolutely crucial, and testing is a critical part of validating this. Simulation will play an increasing role in subjecting these systems to the almost limitless possibilities that can occur on our roads but ultimately these simulated tests will need to be correlated in the real world. Testing will need to encompass every conceivable scenario, driving an increase in the volume of testing as automation becomes more prevalent.
How will testing requirements for automated driving differ from current practices?
Automated driving functions demand new testing methods and tracks. For example, we anticipate that the current single-run approach to testing will need to be replaced by a more efficient fluid solution. Imagine a swarm of vehicles continuously repositioning to perform a multitude of uninterrupted scenarios over hundreds of kilometres on a looped track. We are developing new communication technologies as well as scenario planning and execution tools to enable this type of testing. It will require proving grounds to develop new facilities to allow continuous running on multi-lane highways to meet this type of testing.
How is AB Dynamics preparing for the future of automated driving testing?
We are ready to embrace the future challenges in automated driving testing. As the industry works towards providing safe and affordable automated driving, we are committed to delivering cutting-edge test solutions. Our focus is on adapting to new testing methodologies, developing innovative products, and contributing to the evolution of the automotive testing landscape.
Key takeaways:
- Over the last decade, the need for increased ADAS testing has placed a higher burden on OEMs, test houses, and test equipment.
- Real-world scenarios are often more complex than regulatory and consumer testing, which typically involves only the vehicle under test and a single ADAS target.
- AB Dynamics envisions a shift towards more realistic and complex testing scenarios. Increasing levels of automated driving will necessitate more complex testing.
- Automated driving functions demand new testing methods and tracks. AB Dynamics anticipates that the current single-run approach to testing will need to be replaced by a more efficient fluid solution.
For more information on how AB Dynamics can support your ADAS testing programme visit click here or contact us at info@abdynamics.com.
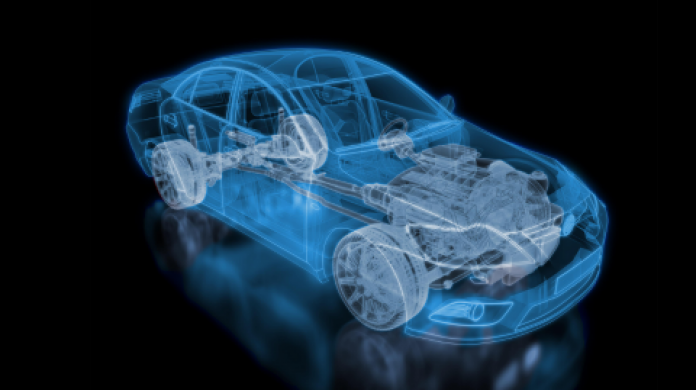
With the adoption and continued growth of electrified powertrains and autonomy the automotive industry is in the middle of a profound transformation. Never before have manufacturers needed to develop so much new technology and it is driving the demand for a more efficient way of testing. At the forefront of this transformation is XiL testing (Everything-in-the-Loop), which encompasses Software-in-the-Loop (SiL), Hardware-in-the-Loop (HiL), Driver-in-the-Loop (DiL) and Vehicle-in-the-Loop (ViL). In this latest blog post, Matt Dustan, AB Dynamics Director, Laboratory Test Systems, explains what exactly XiL is and its potential to reduce the need for prototype vehicles, improve safety, and evaluate the interaction of interconnected systems.
What is XiL?
XiL testing essentially allows the integration of external elements into a simulation to enable a system or sub-system to be thoroughly evaluated. One of the key advantages of XiL testing is the ability to test hardware and software in parallel before transitioning to a prototype vehicle. This early-stage testing enables manufacturers to identify issues and make critical design decisions earlier in the development process than would be possible without XiL testing. The result? Engineering is front-loaded much earlier in the development process to lead to a more mature solution before progressing to prototype vehicles, significantly reducing time-to-market and lowering costs.
In the earlier stages of development, simplified simulations and models can be used but as the design matures it is critical to make them as accurate as possible. Using real hardware in the loop is crucial for achieving precise feedback and accurate correlation between simulations and reality and this is where HiL comes into play. It enables real complete sub-systems to be integrated into the development process, providing precise feedback, and ensuring that simulations correlate with real-world performance.
Interconnected system development
XiL testing also excels in evaluating the interaction of interconnected automotive systems. For instance, our SSTM (Steering System Test Machine) enables a complete steering system to be evaluated and thoroughly tested. Through XiL testing, real steering hardware and software can be assessed using a simulated vehicle model.
As the SSTM is DiL capable, test drivers can provide valuable subjective feedback on steering feel. Previously, this would only be possible once the steering system was fitted into a prototype vehicle much further down the development cycle. Correcting any issues that arise at this stage could be hugely costly. Using the SSTM to evaluate the sub-system as soon as it is available from the supplier helps to de-risk the programme.
Reducing prototypes and improving safety
XiL testing has become vital in improving the robustness of emerging technologies, such as autonomous systems. By collaborating with automotive manufacturers, we have seen the transformative impact of XiL testing in taking immature software toolchains and rapidly enhancing their robustness in a controlled laboratory environment. This not only accelerates development but, particularly in the case of autonomy, reduces the need for extensive on-road testing to improve safety.
The holy grail for the automotive industry is to remove the prototype vehicle stage altogether. Huge investments are made by manufacturers at this point in the programme. We are already seeing stages of prototyping being reduced as a result of simulation and XiL testing, particularly at the sub-system level. However, correlating your simulations with real-world tests is the only way to be truly confident in the results of simulations, so final prototypes are likely to remain a part of the development process for the foreseeable future.
Limitations and the future of XiL testing
There are also certain areas of vehicle development that remain incredibly difficult to simulate accurately in real-time. For example, modelling the behaviour of materials like rubber is complex. As a result, NVH (Noise Vibration and Harshness) is challenging to get right in simulation and as squeaks and rattles can be a common source of warranty issues, it wouldn’t be wise to rely on simulations to validate this. However, we are seeing OEMs actively developing specialised test rigs to better understand and address these complex material interactions.
As the XiL testing process evolves, we are witnessing a shift towards parallel testing, where HiL, SiL and DiL are being utilised at the same time. We are also seeing a move to cloud computing to significantly increase the scale of simulations. The ability to access sophisticated computing power from external providers, hosted in the cloud, is becoming increasingly attractive. This approach is particularly beneficial for automotive startups, allowing them to avoid upfront investment costs and scale their computing resources as needed.
Conclusion
Ultimately, XiL testing is a catalyst for transformation across the automotive industry. It is a critical tool for streamlining development processes, reducing costs and in some cases improving safety. As the industry continues to adopt increasingly sophisticated technologies, XiL testing is now at the forefront of helping manufacturers achieve this in a cheaper, quicker, and more robust way.
The AB Dynamics Group is perfectly placed to support this process as a supplier of products and solutions across the XiL spectrum. With the SSTM and our SPMM, AB Dynamics is providing the industry with state-of-the-art HiL test equipment to thoroughly test and correlate vehicle subsystems. Ansible Motion provides a range of high-fidelity DiL simulators and sister company and simulation software specialist, rFpro, creates highly realistic digital environments for all this testing to take place within.
Key takeaways
As the industry progresses towards virtual development and validation XiL testing will play a key role in providing manufacturers the confidence to remove stages of physical prototypes:
- XiL testing enables the engineering of systems and sub-systems to be frontloaded, reducing cost and accelerating time to market.
- Parallel testing provides highly valuable subjective feedback with the real hardware.
- Some aspects of vehicle development, such as NVH, are challenging to simulate accurately providing a barrier to the complete removal of physical prototypes.
- Advances in cloud computing are allowing testing to be massively scaled and provide start-ups with significant testing capability.
For more information on AB Dynamics' SSTM machine, download our brochure.
With the interest in connectivity and particularly Vehicle-to-Everything (V2X) technology increasing in the automotive industry, Andrew Pick, Business Director of Track Test Systems at AB Dynamics, explains what the technology is, how it would work in practice and how it could significantly improve road safety.
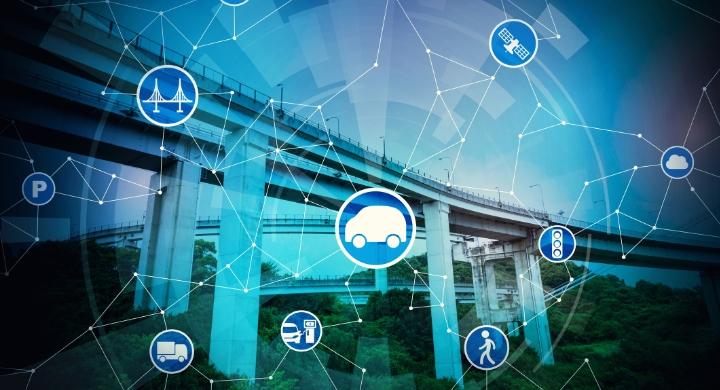
What is V2X technology and how is it benefiting the automotive industry?
In essence, V2X technology enables everything on our roads to communicate together. The aim is to create a collaborative and cooperative capability that enables safety messages to be shared amongst users. It is split up into three different levels; to give information, to increase awareness and to provide warnings.
The key benefit is to improve road safety. By providing vehicles and drivers with more information about their surroundings, they should be more aware of potential hazards ahead and be able to act accordingly.
This technology is seen as an enabler for autonomous vehicles in the future. A lot of what we do as humans when driving is collaborate with other drivers, such as a subtle wave of the hand to allow another car through. Autonomous vehicles need to be able to do this too and V2X is the language they will speak. Except there will be much more information exchanged than could ever be possible with hand signals. For example, you may communicate a hazard ahead to an oncoming driver by flashing your lights. With V2X, the type of hazard and its exact location will be communicated to all nearby vehicles.
How will V2X work in practice?
V2X technology is split up into different elements. For example, Vehicle-to-Infrastructure (V2I) and Vehicle-to-Vehicle (V2V), but also connectivity to other road users.
We are seeing V2V being adopted first as the technology can be integrated relatively easily and rolled out in new vehicle models. For vulnerable road users (VRU) implementation might be based on mobile phone technology and could also be easily integrated into micro-mobility solutions, such as bicycles and electric scooters. Infrastructure, such as traffic lights and variable speed limits, is likely to take more time as these lifecycles are longer and so will need to be upgraded or replaced specifically. In time though, as the network increases, the bigger and more powerful it becomes.
These elements will be continually broadcasting a cooperative awareness message (CAM) or a decentralised environmental notification message (DENM). The CAM provides information such as speed, position and heading of other vehicles. The DENM communicates information on accidents or other hazards on the road.
What are the current limitations of the technology?
As with any new technology, consumer acceptance is key to success. A vehicle equipped with V2X will be receiving a huge amount of data. A driver doesn’t want to be made aware of every single vehicle nearby, only the safety critical information. Deciding what information to share with the driver and how will be critical.
The biggest question for the industry is what “language” should be used. For it to work effectively it must be universal across the elements. Currently, there are two competing standards. ITS-G5 is an ad hoc Wi-Fi, which has already been adopted by Volkswagen and can be found on the latest Golf and all its ID models. The alternative is cellular V2X, or C-V2X, which essentially piggybacks off the existing mobile phone networks, such as 4G and 5G. This choice is a critical crossroad for the industry as manufacturers won’t want to back the wrong horse.
The greatest limitation of the technology though is adoption. For it to have a powerful effect it needs to be on as many vehicles as possible, as well as being built into the surrounding infrastructure. Although legislation is effective by mandating the technology the time scales are long. Consumer tests provide a powerful alternative and Euro NCAP has identified V2X technology as a key safety enabler in its recent roadmap for 2030. This provides great motivation for vehicle manufacturers to adopt the technology more widely.
How quickly are we likely to see V2X technology integrated into Euro NCAP testing?
We don’t know the answer yet. But it is anticipated that Euro NCAP will include a level of V2X in the next protocol update, which is due in 2026. Euro NCAP has stated that it intends to accommodate all forms of connectivity by evaluating safety functions in a technology-neutral way. This essentially means these communications systems will form part of the Euro NCAP test scenarios, regardless of which “language” is used.
They have highlighted a staged rollout of the technology testing. The first is improving driver awareness using V2X by giving warnings to drivers of potential hazards. This is relatively quite easy to test as it is essentially an advanced level of the safety assist features that Euro NCAP currently use, such as speed assist.
The second phase is the use of V2X to proactively avoid collisions, perhaps where there are obstructions out of sight of conventional ADAS sensors. V2X could be used to track that object throughout the test scenario. Again, this wouldn’t be a big challenge as it would complement scenarios that Euro NCAP is already testing.
For example, imagine a scenario where a vehicle operating under assisted driving on a highway is suddenly presented with a stationary vehicle in the lane ahead that was obscured by a lead vehicle, which suddenly cuts out into the adjacent lane. Currently, the assisted vehicle would rely on an AEB (Automatic Emergency Braking) system to prevent a collision. By the very nature of how the system works this would involve a last-minute emergency manoeuvre, which is uncomfortable and unsettling for the vehicle’s passengers and other traffic. With V2X, the assisted vehicle would be forewarned of the hazard and would slow down in a controlled and timely manner.
By providing the vehicle with information earlier it moves the necessary action further down the road to give the vehicle much more time to react. This technology has the potential to improve road safety by significantly reducing the number of collisions.
How will AB Dynamics be helping the industry test the technology and these new test scenarios?
If you want to thoroughly test the technology, it needs to be done in a controlled and repeatable way on a proving ground. As a result, we are adding connectivity to our range of ADAS test platforms. This allows us to augment connectivity during tests so that connected targets and test objects broadcast the same digital signature as a real vehicle would on the public road.
To effectively test connectivity, it needs to be built into the test scenarios. In the same way that we currently define the path and speed of the vehicle, we will also need to define the messages the vehicle broadcasts. To enable this, we have integrated connected hardware to our products which communicate the CAM and DENM information of our targets and the navigation system directly. This is linked to the test scenario, via our software, so we can define the message and the trigger point on demand. We can also log the V2X messages that are being broadcast by other vehicles and the test objects.
We have also developed the connectivity solution to be retrofittable to existing products and to support both the ITS-G5 and C-V2X communication technologies. In fact, the ITS-G5 technology is very similar to what we use on the proving ground already to communicate between the test vehicles and ADAS targets. So, we already have a lot of experience with this technology.
This is a new capability for us. We have already started demonstrating it as part of one of the work packages in the SECUR (Safety Enhancement through Connected Users on the Road) project.
Can you tell me more about the SECUR project? What is the objective?
The SECUR project, coordinated by UTAC, aims to create a coherent proposal for V2X testing and assessment protocols for Euro NCAP. It brings together a consortium of 20 international stakeholders from the entire automotive and V2X ecosystem, who will share knowledge and collaborate through workshops and working groups. Together with AB Dynamics, the partners include Volkswagen, Honda, Toyota, Denso, Bosch and Continental. Our key input into the project is to help define a specification for connected targets to support this testing in the future.
To learn more about the SECUR project, visit https://www.utac.com/documents
Over the past decade the increased usability and capability of multi-physics simulation tools available to engineers has created a valuable opportunity for more accurate, better informed, and faster product development. This trend is well encapsulated in the recent industry buzzword the ‘digital twin’ which describes virtual replicas of complete physical systems that engineers can use to run simulations before new hardware or hardware updates are built and deployed.
However, experience of a product life cycle will quickly expose the practicality that complete reliance on simulation in development will almost inevitably fail. The unexpected vagaries of the real world driven by incomplete information and the difficulty of capturing all significant influences in a mathematical description of a system require repeated correlation of models to the real world through physical testing
The digital twin must not remain the poster child of the trade show banner or a friendly companion in the clean and dry development office but must be put through its paces on the rain swept test track and given a workout in the oily, noisy test lab. The more novel the simulation, the more it requires a shakedown against reality to check the equations and input parameters. Is a material supplier’s data written by an optimistic marketeer or a cautious stress engineer? Is the thermal performance of an assembly dominated by the materials or the joints between the materials? How much confidence can you have in those long 3D eddy current simulations?
The higher value second pay back of a well correlated model, that accurately describes what is actually happening in a first prototype or existing product, is delivered when tested data and equations are used in the development of the actual product or a second generation device, and when variants and new ideas can be tested with greater confidence in the virtual environment.
With the SPMM product, AB Dynamics has for 25 years provided the international automotive industry with a class leading tool to accurately collect whole vehicle correlation data for ride, handling, and suspension development. In controlled lab conditions the kinematics and compliance of the complete body and suspension assemblies can be quickly and accurately measured and logged.
Adding to this automotive development tool capability, AB Dynamics has recently launched the ANVH 250 product which achieves a similar characterisation task for the axle sub assembly. A complete axle system can be loaded into the machine and tested for road noise transmission from the wheel to the body mounting points. The additional capability of axle level kinematics and compliance measurement allows the impact on ride and handling performance to be tracked as NVH requirements are achieved through bushing compliance and suspension element natural frequency modifications.
Axle NVH issues often remain undetected until late in a vehicle program, which leads to expensive corrective measures, additional weight or sub-optimal designs being carried into production. Adding the ability to test the sub assembly hardware, feed correlation data back to the sub assembly model and tune the axle system prior to inclusion in the vehicle prototype allows optimised assemblies to be delivered into the development programme designed and tested to a predefined performance specification.
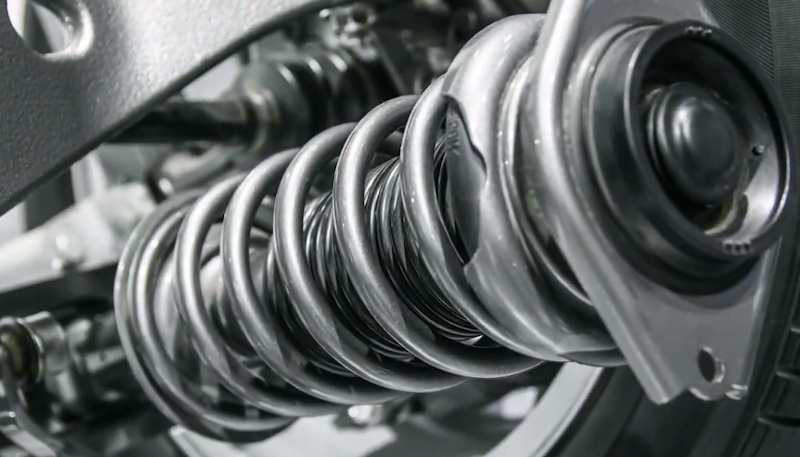
Rapid advances in simulation methods means an increasing amount of vehicle development testing is now being undertaken in the virtual world.
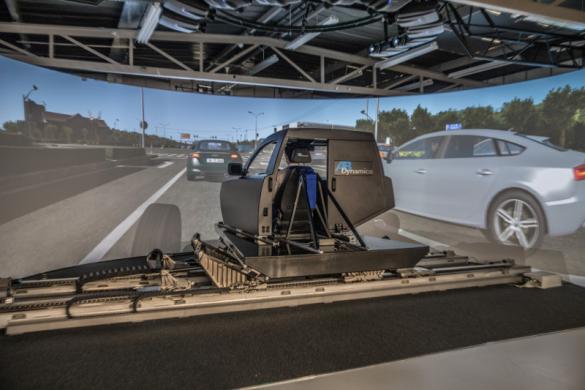
The increase in vehicle system complexity associated with Connected and Autonomous Vehicles means completing the required tests in the ever-shortening time available, is a major challenge for vehicle manufactures. In addition, the number of tests requested by international test standards agencies like Euro NCAP and NHTSA has increased significantly in recent years. The result is increased pressure to find efficiencies through virtual testing.
The ability to build highly accurate vehicle models and to test these in high fidelity virtual environments including proving grounds and road networks means that the test driver can now drive a virtual prototype of the vehicle and feed into the development process long before a physical prototype has been built. This reduces both development time and costs as repeatable test results can be obtained earlier in the development cycle and in greater depth than previously possible using physical prototypes.
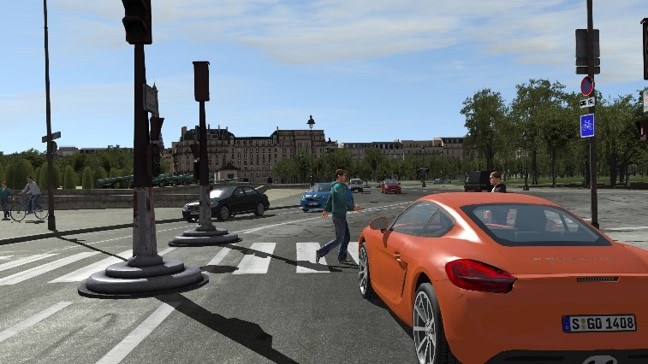
The AB Dynamics advanced Vehicle Driving Simulator (aVDS) contains a class-leading third generation motion platform with high response, low latency, low noise and large payload capacity. The class leading dynamic performance of the platform means that virtual testing of vehicle ride and handling is no longer constrained by the physics of the motion platform.
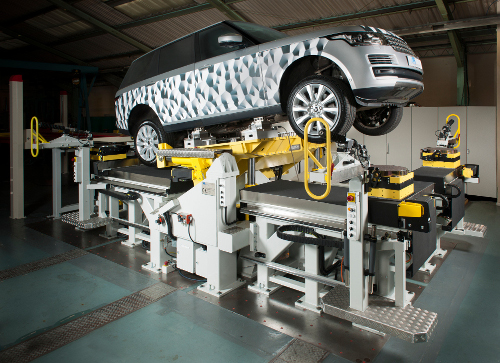
AB Dynamics suite of products includes systems for virtual, lab and track testing. Compatibility and synergy between the products is designed to minimise the workload faced by engineers as they move from one environment to the other. For example K&C data generated by the SPMM can be imported directly into the CarSim and CarMaker models driven on the aVDS. Likewise the ADAS test scenarios driven virtually on the aVDS may be easily validated physically on the track using AB Dynamics suite of ADAS soft crash targets, with consistency ensured by using the same robot controller software and hardware in both the physical and virtual environments.
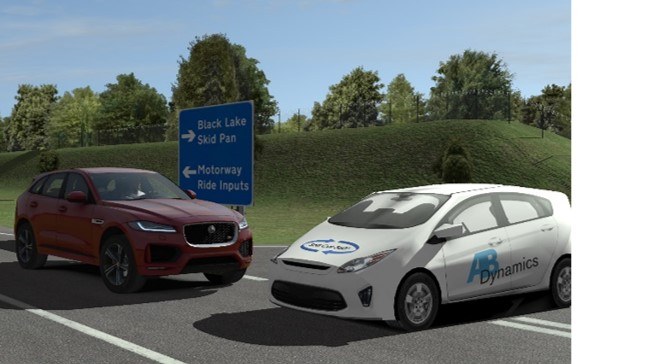