Over the past decade the increased usability and capability of multi-physics simulation tools available to engineers has created a valuable opportunity for more accurate, better informed, and faster product development. This trend is well encapsulated in the recent industry buzzword the ‘digital twin’ which describes virtual replicas of complete physical systems that engineers can use to run simulations before new hardware or hardware updates are built and deployed.
However, experience of a product life cycle will quickly expose the practicality that complete reliance on simulation in development will almost inevitably fail. The unexpected vagaries of the real world driven by incomplete information and the difficulty of capturing all significant influences in a mathematical description of a system require repeated correlation of models to the real world through physical testing
The digital twin must not remain the poster child of the trade show banner or a friendly companion in the clean and dry development office but must be put through its paces on the rain swept test track and given a workout in the oily, noisy test lab. The more novel the simulation, the more it requires a shakedown against reality to check the equations and input parameters. Is a material supplier’s data written by an optimistic marketeer or a cautious stress engineer? Is the thermal performance of an assembly dominated by the materials or the joints between the materials? How much confidence can you have in those long 3D eddy current simulations?
The higher value second pay back of a well correlated model, that accurately describes what is actually happening in a first prototype or existing product, is delivered when tested data and equations are used in the development of the actual product or a second generation device, and when variants and new ideas can be tested with greater confidence in the virtual environment.
With the SPMM product, AB Dynamics has for 25 years provided the international automotive industry with a class leading tool to accurately collect whole vehicle correlation data for ride, handling, and suspension development. In controlled lab conditions the kinematics and compliance of the complete body and suspension assemblies can be quickly and accurately measured and logged.
Adding to this automotive development tool capability, AB Dynamics has recently launched the ANVH 250 product which achieves a similar characterisation task for the axle sub assembly. A complete axle system can be loaded into the machine and tested for road noise transmission from the wheel to the body mounting points. The additional capability of axle level kinematics and compliance measurement allows the impact on ride and handling performance to be tracked as NVH requirements are achieved through bushing compliance and suspension element natural frequency modifications.
Axle NVH issues often remain undetected until late in a vehicle program, which leads to expensive corrective measures, additional weight or sub-optimal designs being carried into production. Adding the ability to test the sub assembly hardware, feed correlation data back to the sub assembly model and tune the axle system prior to inclusion in the vehicle prototype allows optimised assemblies to be delivered into the development programme designed and tested to a predefined performance specification.
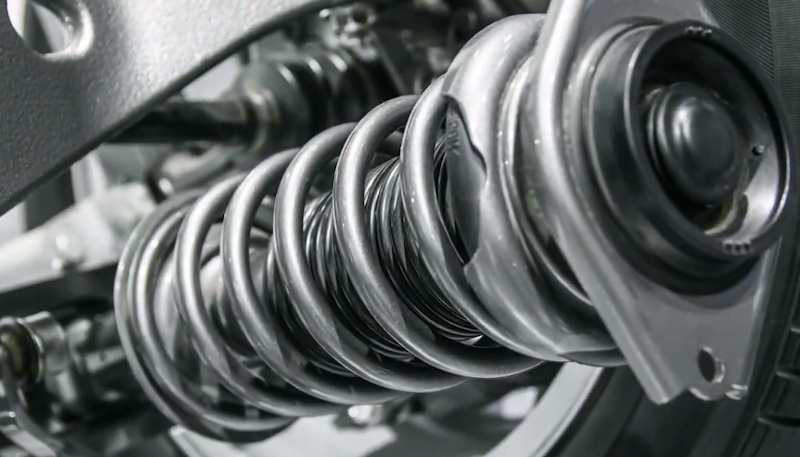