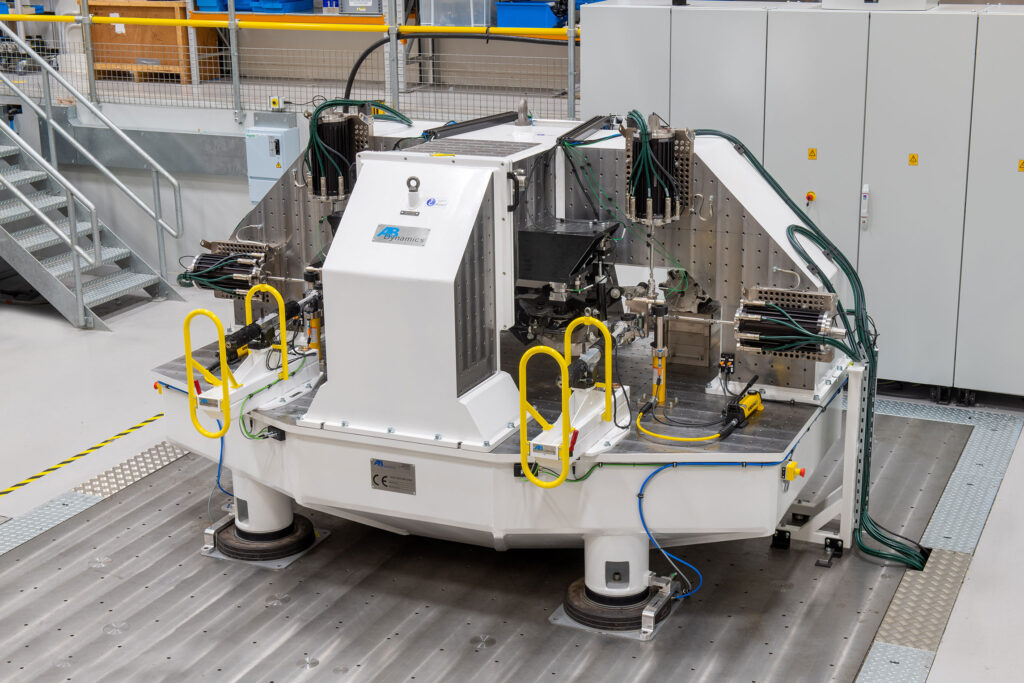
Suspension system NVH testing
Optimising noise, vibration, and harshness characteristics early in the design process.
What is NVH?
Noise, vibration, and harshness (NHV) is a field dedicated to the analysis and mitigation of noise and vibration attributes in vehicles. It’s a critical aspect of vehicle design, affecting both performance and user experience. NHV testing involves exposing a complete vehicle, or a component or subassembly to vibrations across various frequencies. This helps in identifying potential issues or annoyances.
NVH issues can often remain undetected until late in a vehicle development programme, which can lead to costly and compromised corrective measures. Our ANVH 250 test machine enables accurate measurement of suspension system NVH transmission long before prototype vehicles are available.
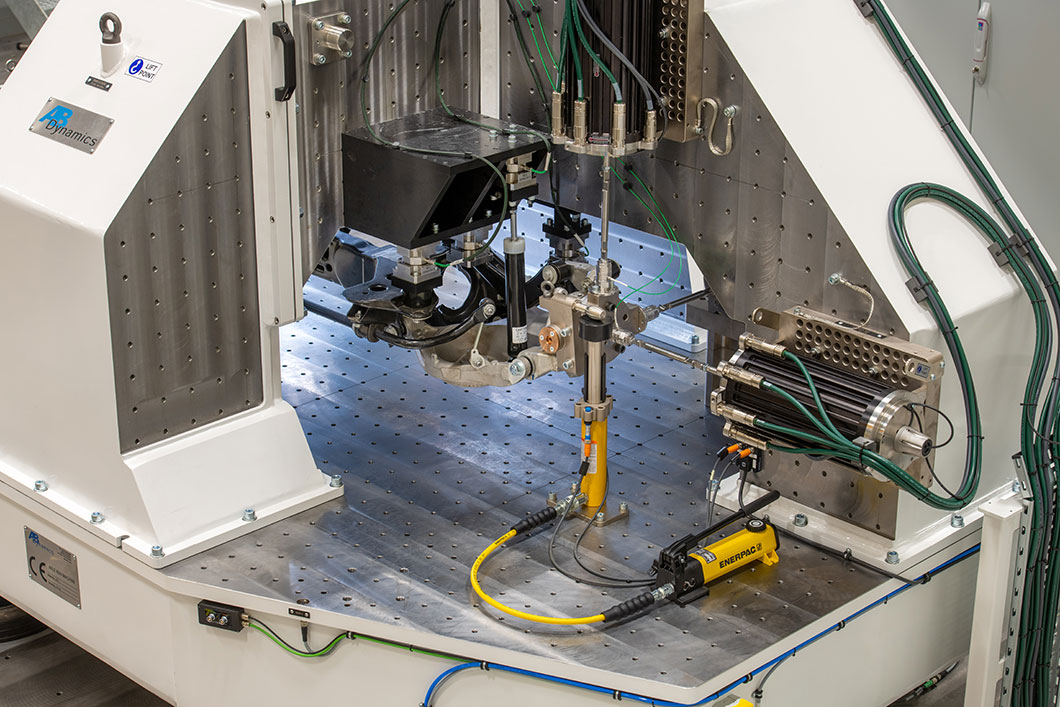
The ANVH 250
The ANVH 250 measures the transfer path of structure-borne noise induced by a vehicle suspension’s interaction with the road surface early in the development process. The ANVH 250 is designed to allow a wide range of vehicle sub frame assemblies to be loaded and fixed to the frame with custom mounts. It also has the option to be fitted with the Dynamic Arm wheel position measurement system from our SPMM Plus to enable basic kinematics and compliance (K&C) characteristics of the axle subframe to be measured.
How the ANVH 250 works
The ANVH 250 simulates the structural propagation of vibrations from the tyre contact patch through the suspension system to the vehicle body by injecting high-frequency test signals into the axle spindles. Up to six bespoke electro-magnetic actuators apply precisely controlled motion at frequencies from 0-250Hz and displacements from +/-0.01 to +/-50mm, while tri-axial load cells measure the forces transmitted to each vehicle body mounting point.
The ANVH 250 can apply sinusoidal, random input and road load data displacements to the suspension system. Displacements can be applied to the wheel hubs in the vertical (Z), longitudinal (X) or lateral (Y) directions. The paired displacements at the hubs can be in-phase, anti-phase or single-sided. By analysing the resultant forces, accelerations and displacements, sources of structural resonance can be identified, isolated and optimised.
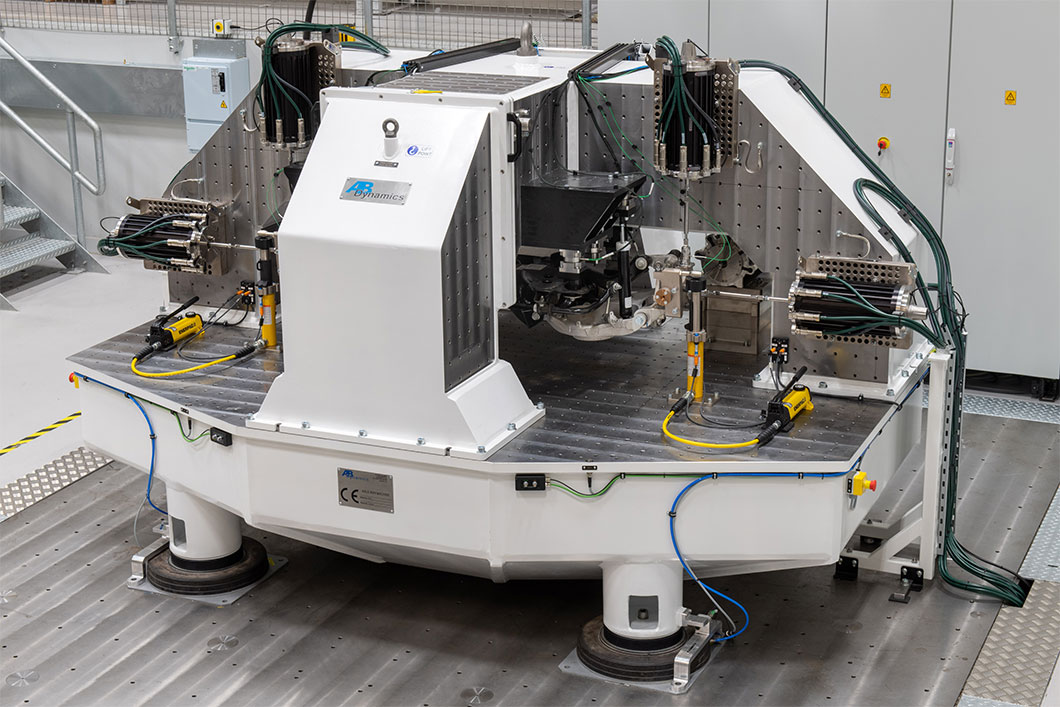
Specifications
The changing automotive landscape is making it more important than ever to get NVH right. The ANVH 250 solution includes the following features:
- Closed loop control 0-250Hz
- All electric design
- Up to 10 kN pneumatic pre-load per actuator
- Up to 10 kN peak force per actuator
- K&C testing option
- Accommodates a wide range of subassembly types and sizes
Get the ANVH 250
"*" indicates required fields
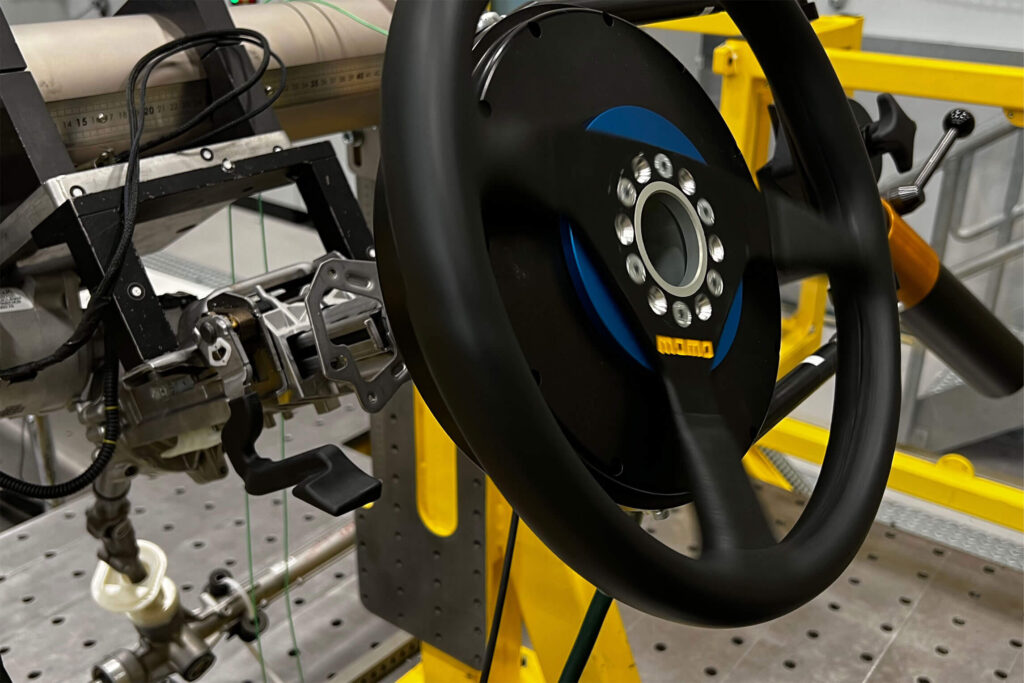
Steering system test equipment
Turning the art of steering development into a science.
Steering system development
The steering system is an important system to a car’s design as it affects the vehicle’s handling, stability, comfort and safety. However, to achieve the desired steering feel, steering system testing typically relies on physical prototypes and track testing, which are costly, time-consuming, and subject to environmental and human factors. Moreover, due to emerging trends in the automotive industry such as electrification, automation, and personalisation, more advanced and flexible steering system testing solutions are required. This is why AB Dynamics has developed laboratory steering system test equipment that can precisely replicate real-world conditions to help accelerate the steering system design process.
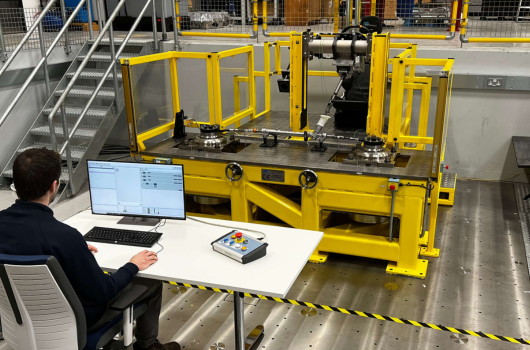
The SSTM
The SSTM is an advanced steering system test machine that enables characterisation, mechanical hardware-in-the-loop (mHiL) and driver-in-the-loop (DiL) activities to be completed on hydraulic, electric power assisted steering (EPAS) and drive-by-wire steering systems. It offers a controlled laboratory environment for assessment, characterisation, and optimisation of steering systems in isolation from the vehicle under development. By subjecting steering systems to simulated independent tie rod forces it precisely replicates real world conditions with minimal latency. With the SSTM, you can accelerate the steering system design process by identifying issues early, reduce costs and deliver an enhanced final product.
How the SSTM works
The SSTM consists of two mounting tables with a high resonance frequency of greater than 150Hz. The front table contains two rotary wheel actuators, one either side of the steering system, and the steering rack mount. The rear table houses the steering column mount, the steering robot and the driver chair. The SSTM uses our industry-leading driving robot to apply inputs into the steering column. To best simulate the geometry of a vehicle, the SSTM uses high-frequency, high-torque rotary wheel actuators to replicate tie rod forces as the inputs into the steering system and highly accurate piezoelectric load cells to measure the resultant forces from the machine.
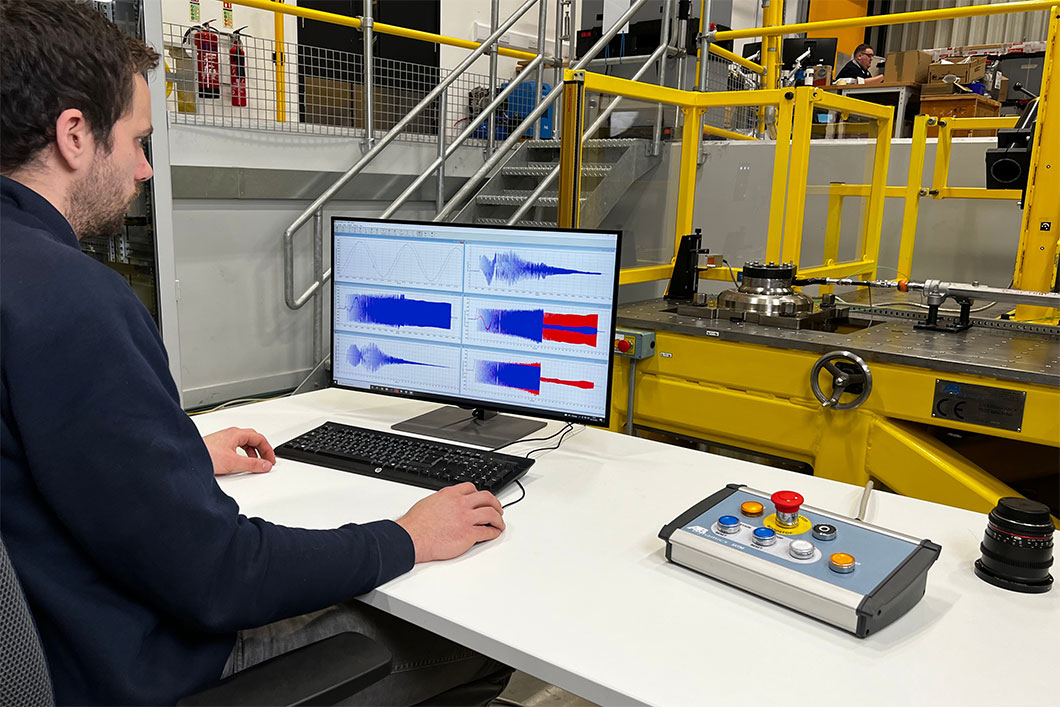
Access immersive testing with a static driving simulator option
With the integration of Ansible Motion’s driving simulator technology combined with rFpro’s simulation environment and visuals, the SSTM becomes a highly advanced driving simulator with the steering hardware fully incorporated. This offers a multitude of benefits especially for ADAS development in Hardware-in-the-Loop (HiL) and Driver-in-the-Loop (DiL) testing. The seamless setup of the steering system and the driver chair to achieve correct vehicle-matched geometry ensures a highly immersive environment for test drivers to subjectively assess the real steering system in simulation. By conducting complex simulated scenarios in the laboratory, you can save significant setup time and costs typically associated with track testing.
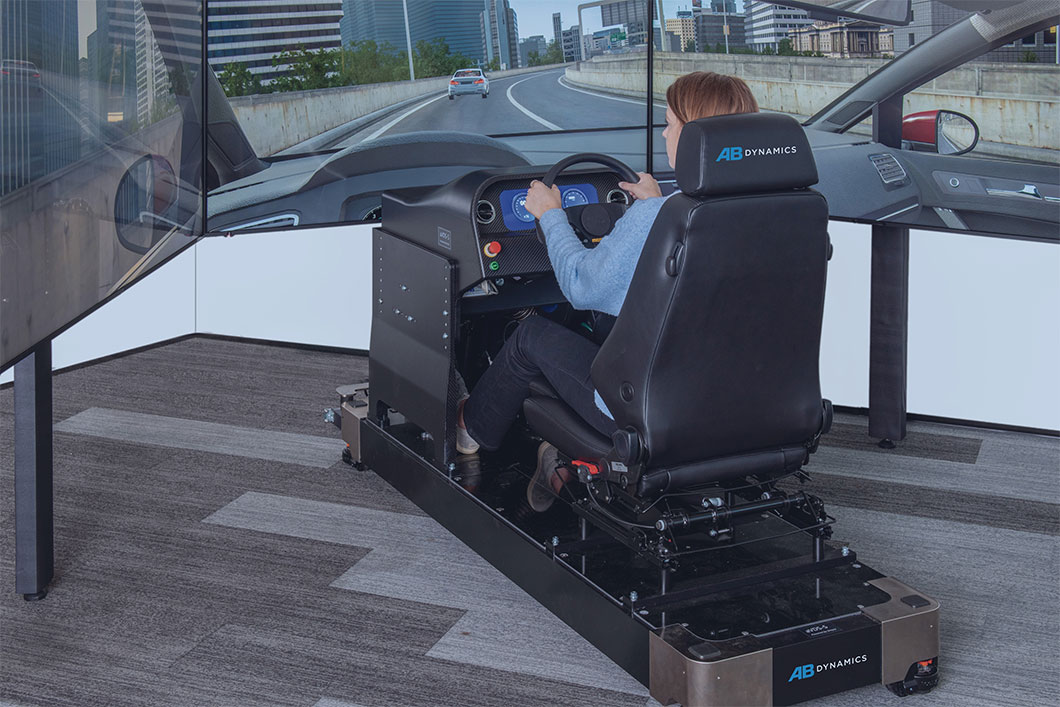
Key features and specifications
- Compensated dual sided tie rod force control for accurate command following
- >40Hz tie rod force control bandwidth
- Electromechanical actuators provide a clean work environment and minimal maintenance
- High natural frequency tables and actuators in excess of testing frequencies
- mHIL capability enables the physical steering system to bypass the steering model during real-time simulations
- Fast changeover between steering robot and OEM wheel for DiL testing
- Drive-by-wire compatible
- Accurate representation of steer system geometry including inner and outer ball joints
Get the SSTM
"*" indicates required fields
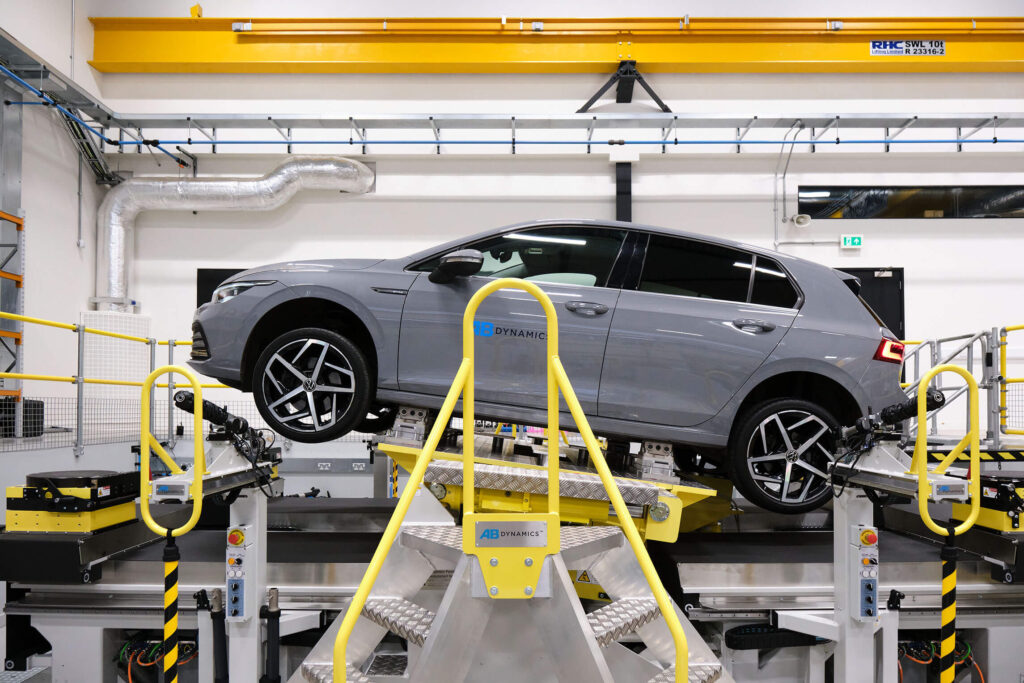
CoG and MoI test equipment
Precise and efficient measurement of Centre of Gravity (CoG) and Moments of Inertia (MoI) for both full vehicles and vehicle components.
Why is accurate CoG and MoI testing important to vehicle development?
The CoG represents the point where the entire weight of a vehicle is concentrated and MoI describes how mass is distributed around different axes of rotation. When developing vehicles understanding and optimising the CoG and MoI are fundamental for creating vehicles that are stable, agile, and safe to handle during real-world driving. The MoI and CoG of a vehicle can be measured using several methods, depending on the level of accuracy and complexity required.
At AB Dynamics, our approach to CoG and MoI testing is via an optional add-on to our Kinematics and Compliance (K&C) test machine, the SPMM Plus. The option permits the measurement of the full mass inertia properties of vehicles and objects, in addition to a detailed analysis of a vehicle’s suspension characteristics under various loading conditions.
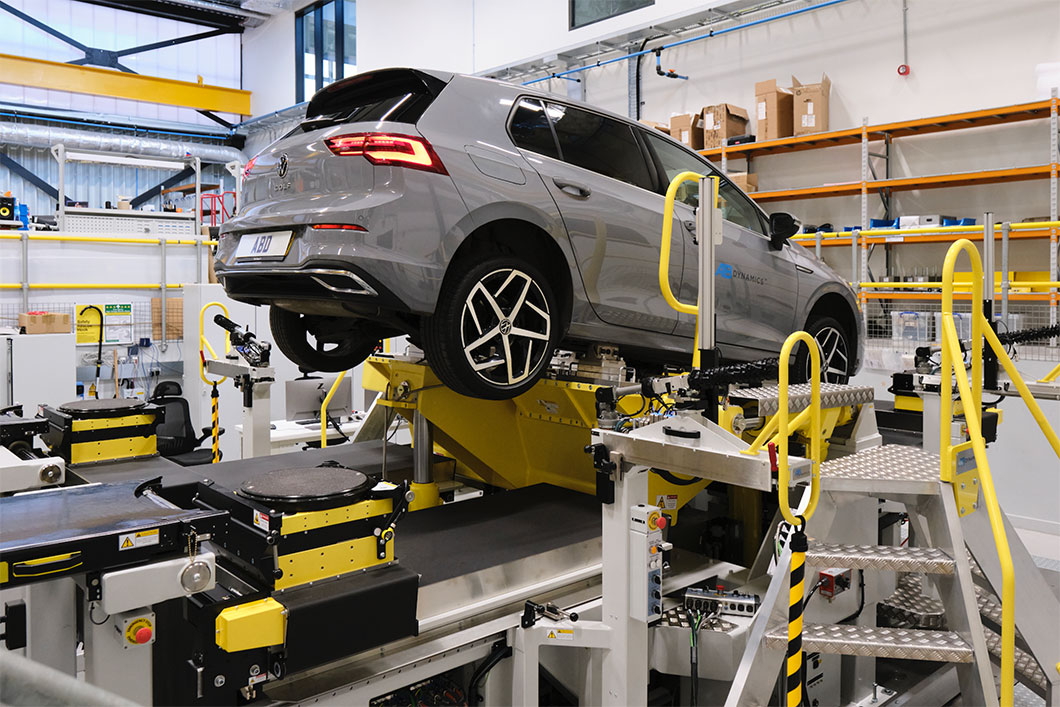
The SPMM Plus
With our Moment of Inertia Measurement System (MIMS) option the SPMM Plus is two machines in one. MIMS allows accurate measurement of CoG and principal MoI for full vehicles and vehicle components, while also being able to generate all the chassis-based data necessary for the creation of digital vehicle models in just a few hours.
The SPMM Plus is the only system to lift, roll and tilt the vehicle to derive the full moment of inertia properties, which are critical to creating an accurate digital vehicle model. In addition to this our MIMS object add-on provides the capability of measuring CoG and MoI properties of standalone objects, such as electric drive units.
How the MIMS upgrade works
The moving body design of the SPMM Plus allows roll, pitch, bounce, and yaw motions to be applied to the vehicle body. This generates forces that are accurately measured using load cells located in the sill clamps. The simplicity of the moving body design also means the SPMM can be changed from K&C to MIMS measurement mode in less than 30 minutes, without the need to unload the vehicle. The MIMS option is available as an upgrade for both two and four-wheel station arrangements.
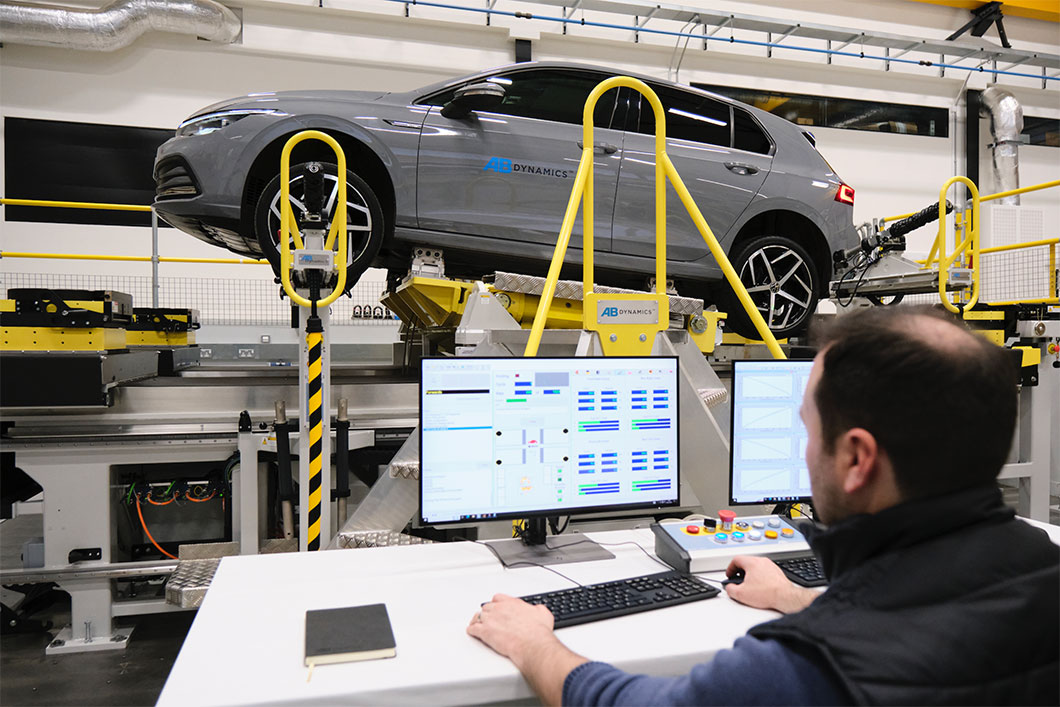
Key features and specifications
- A unique moving body, fixed ground plane design
- Rotations are applied about measured CoG reducing parallel axis errors
- Vertical, roll and tilt tests provide two or more independent measurements of CG X,Y,Z for increased accuracy
- All cross products of inertia can be accurately determined
- Changeover from K&C to MIMS measurement mode takes less than 30 minutes
- Piezoelectric load cell sensitivities specially selected for the MIMS application
- Measurement of standalone objects possible with Object add-on
Get the MIMs upgrade
"*" indicates required fields
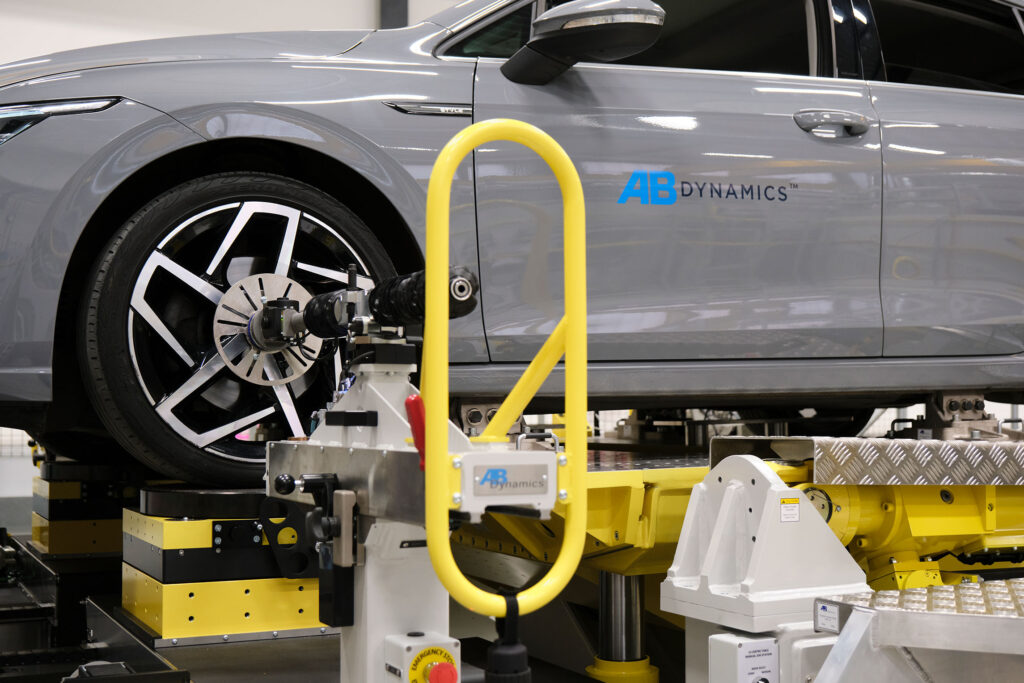
Kinematics and compliance (K&C) test equipment
Transforming information into usable data.
What is kinematics and compliance (K&C) testing?
Kinematics and compliance (K&C) testing is a specialised form of suspension testing that involves applying real-world loads and displacements to a vehicle’s chassis and tyres. The goal of K&C testing is to ascertain the geometry and stiffness characteristics of the vehicle’s suspension system under quasi-static conditions. A K&C test machine provides a thorough understanding of a vehicle’s kinematic and compliance characteristics by applying simple but very accurate inputs. The resulting data informs on the vehicle’s ride and handling characteristics.
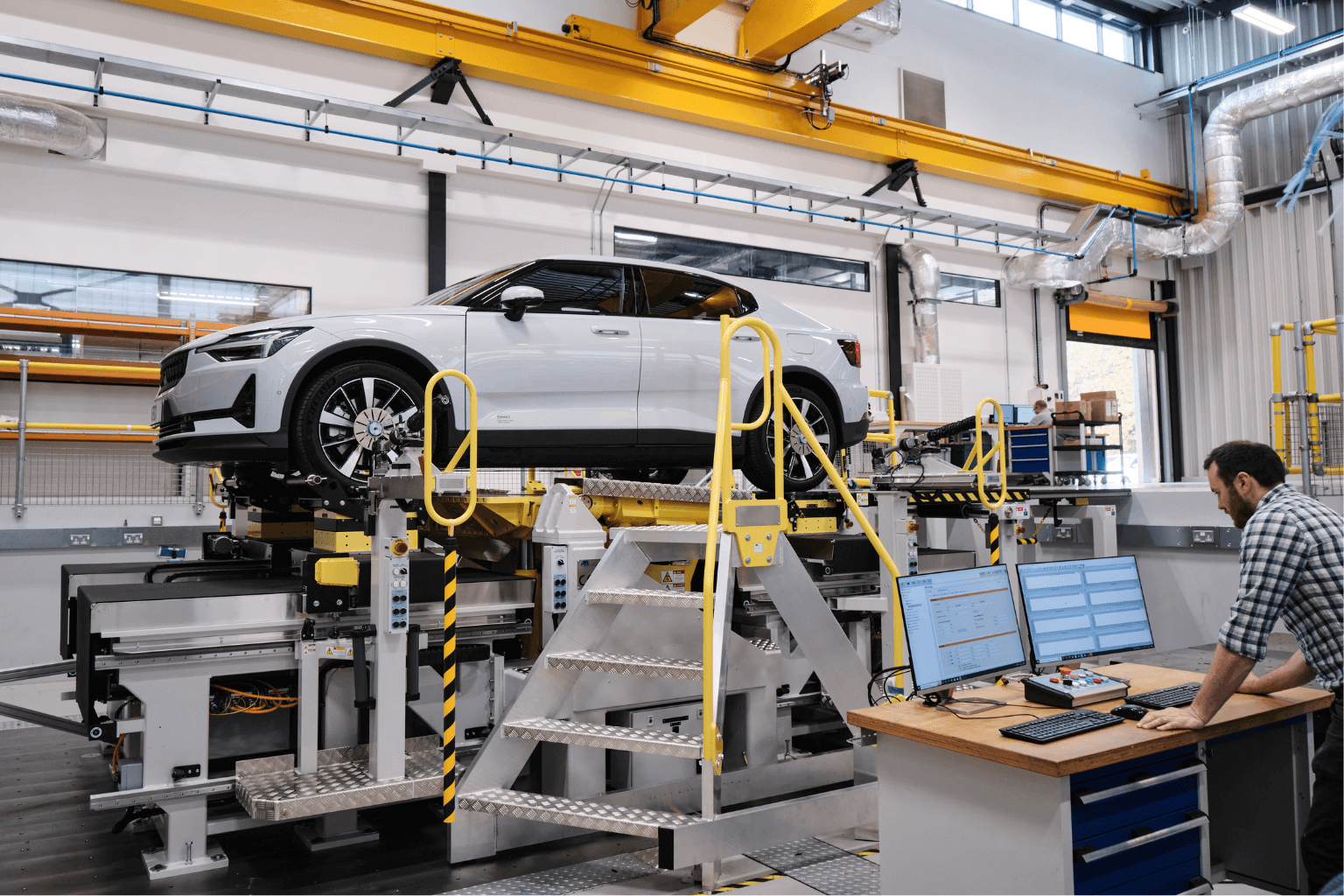
The SPMM Plus
Delivering unrivalled measurement accuracy, the SPMM Plus is the industry’s most technically advanced, reliable, and cost-effective K&C test machine.
Designed around the core principle of faithfully simulating on-road vehicle behaviour, the SPMM Plus is the industry’s most technically advanced, reliable, and cost-effective K&C test machine. Accommodating the smallest city cars up to light commercial vehicles, its unique moving body and fixed ground-plane design replicates a vehicle’s interactions with the road surface with unrivalled precision. It provides all the suspension and steering system data you need to develop vehicles that outperform your competitors.
How the SPMM Plus works
The SPMM Plus has two key areas of measurement: wheel position and wheel force. The test vehicle is clamped to the table and suspension kinematics are analysed by moving the table to simulate the motions of the vehicle body that occur on the road. The resulting wheel centre movement is measured using our Dynamic Arm measurement system, whilst controlling the tyre contact patch loads to zero.
To measure compliance, horizontal inputs are applied at the tyre contact patch by the wheel stations. The wheel stations apply these loads by moving longitudinally (X), laterally (Y) and rotationally (δ). Forces and displacements are measured by the wheel stations integrated piezo-electric load cells.
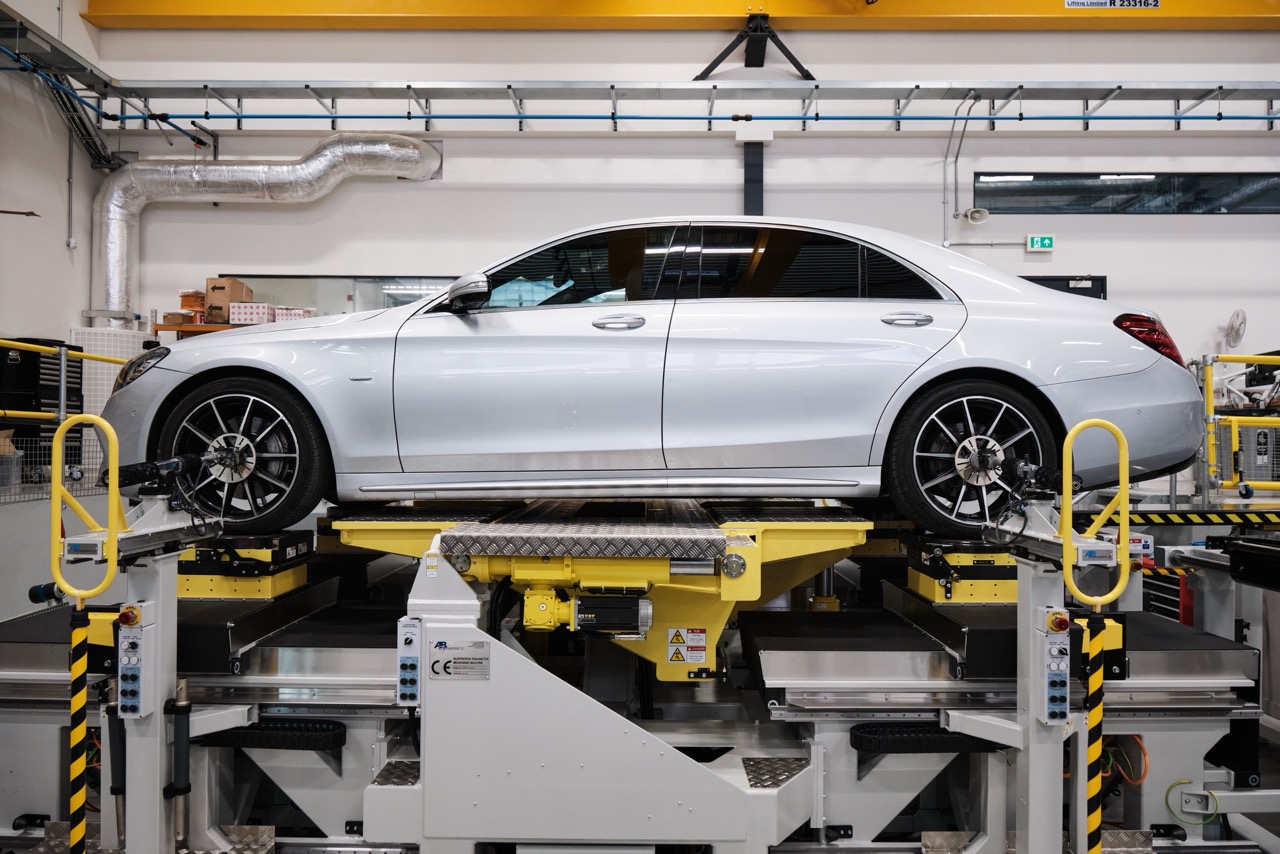
Key features and specifications
- A unique moving body, fixed ground plane design
- Exceptionally accurate Dynamic Arm wheel position measurement system
- Low maintenance, servo-electric design
- Optional Moments of Inertia (MoI) and Centre of Gravity (CoG) measurement capability
- Hybrid simulation data pipe for HiL test capability
- One-click data export to popular modelling packages such as CarMaker and CarSim
Get the SPMM Plus
"*" indicates required fields